From the idea of interchangeable parts popularized in the United States by Eli Whitney for muskets and Henry Ford’s mass production techniques to Japan’s “kaizen” (continuous improvement) methodologies, and techniques like LEAN and AGILE, manufacturers are always on the lookout for ways to improve – increase yields, shorten raw-materials-to-finished-product times, reduce waste, and more.
One new major enabler for manufacturing improvements is the use of computers, ranging from monitoring sensors to “big data” analytics, along with programmable robotic tools. Collectively, these are known as “Smart Manufacturing” and also as “Industry 4.0.”
Here’s a quick look at some of the benefits and opportunities that Industry 4.0 can offer to hardware entrepreneurs, start-ups, and small companies (as well as to larger and more established ones).
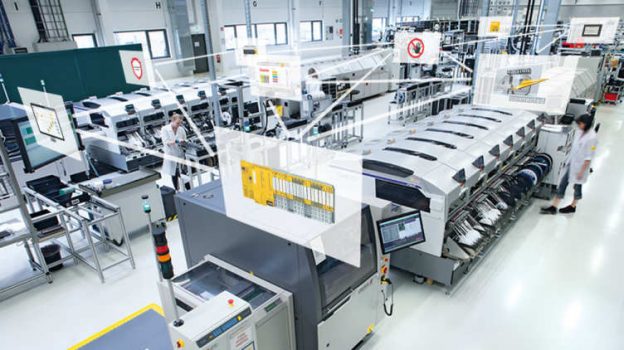
Industry 4.0 and Smart Manufacturing are providing manufacturers with the tools to become leaner and more efficient.
Industry 4.0, Smart Manufacturing – What Are They?
“Industry 4.0 is the current trend in manufacturing that involves a combination of cyber-physical systems, automation and the Internet of Things (IoT), which together create a smart factory,” says Manuel Grenacher, CEO, Coresystems, an SAP company, and provider of cloud-based field service and workforce management software for mid-sized and large enterprise field service organizations.
Industry 4.0 “is all about speed, accuracy, and efficiency,” says Faith Kubicki, Content Marketing Manager, IntelliChief, LLC, which builds workflow automation software for manufacturers and distributors.
According to Kubicki, manufacturers that invest in these types of automation can usually achieve:
- Shorter lead times
- Faster order processing cycles, due to, for example, an order being processed automatically instead of waiting for an employee to manually type them into their order processing system. From there, engineering change orders and other related documents are able to move directly from one department to the next, avoiding communications lag time.
- Lower DSOs (Daily Sales Outstanding) and, as a result, better cash flow.
While these methods, technologies and benefits are usually discussed in terms of large companies and rapidly-scaling product demand, they can also offer significant benefits to hardware entrepreneurs and start-ups, often still working towards the first run of a first product.
“3D printing and other ‘smart manufacturing’ technologies can be a godsend to the typically cash-strapped entrepreneur, whether they invest in equipment directly or rely upon vendors to supply parts,” says Dan Erickson, Application Engineer, Fisher Unitech, a provider of SOLIDWORK 3D design software tools and Stratasys 3D printers.
“‘Smart manufacturing’ is all about flexibility and decentralization,” says Erickson. “This leads to more producers in more places, and to producers who are able to make small batches of parts on-demand. That allows entrepreneurial manufacturers to provide a wider variety of products to a wider customer base, and allows startups to fail faster, testing iterations faster than ever before.”
This kind of flexibility makes possible improved and new products, and makes it possible for new, smaller companies to create them.
For example, according to Sarah Boisvert, Founder of Fab Lab Hub LLC, a workforce training content provider, and author of The New Collar Workforce:
- Industry 4.0 factories embracing 3D printing and additive manufacturing can do mass customization, and complex geometries. AirBus is reporting a 55 percent reduction in weights in parts that they 3D print with complex geometries.
- For a product design, say, a hinge, “You can make ten and try them – or run ten different designs and versions. The swapover time is easy, you just change it in CAD – since you’re doing 3D printing, you don’t have to make a mold.”
But, says Boisvert, what’s more interesting about Industry 4.0 versus traditional CAD, is “the factory-as-a-system.”
“When you send your design to the manufacturer, they can not only put the design through the manufacturing process, but they can create a ‘digital twin’ which gets run through a simulation,” Boisvert. “This lets you see it as it is in the process, and gives you the chance to optimize both the design for manufacturing, and also optimize the process as it goes along.”
For hardware startups, these new capabilities are great news. You’ll have more opportunities to tweak and fine-tune your design, which should in turn let you get a better product ready for quantity production sooner and less expensively.
You might like: The Documents You Need to Progress to Manufacturing
Be the first to post a comment.