What goes into a “good” design?
That’s a very good question, and one we typically have to deal with in the additive manufacturing business on a daily basis. With 3D printing, a good design is more than its aesthetics, it must consider functionality, cost, time and repeatability.
At Stratasys Direct Manufacturing, we have identified four elements to balance in order to build the ideal part: size, resolution, wall thickness, and build orientation. The combination of these elements will reveal the ideal formula for you to get both the ultimate functionality and aesthetics out of your part.
Now, let’s delve a little deeper into each of these key factors that will make up your ideal design:
Size
One key consideration to keep in mind when designing for additive manufacturing is the size of your part. Each of our 3D printing technologies have an optimal build space, but some are larger than others. The largest build volume is available on our Fused Deposition Modeling (FDM) 3D printers at 36”x24”x36” (X, Y, and Z).
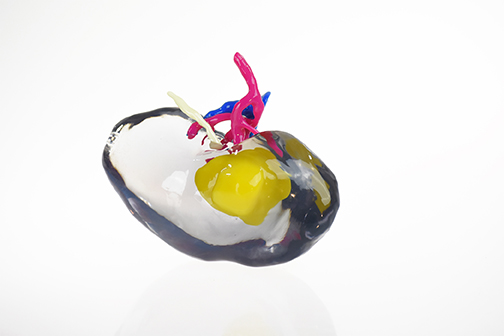
PolyJet technology has the smallest resolution possible with the greatest amount of detail, allowing for highly cosmetic parts.
If your part is larger than that, though, there is no need to worry. Parts larger than the available build volume can be sectioned prior to manufacturing in CAD and seamlessly bonded together post-build. The size of any part and the minimum feature size affects the amount of time it will take to build– a larger part takes longer to build and requires more material, both of which will add costs to your final part. PolyJet technology has the smallest resolution possible with the greatest amount of detail, allowing for highly cosmetic parts.
Resolution
Layer resolution is the thickness of each slice or “layer” laid down during the 3D printing process. Resolution contributes to the surface quality and definition of the part before post-processing. The thinner the layers, the finer the details and smoothness, but the longer the build time.
PolyJet technology will give you the smallest resolution possible with the greatest amount of detail, as small as a layer resolution of .00063”. Stereolithography (SL) also achieves a thin resolution at .0002”, while Laser Sintering (LS) can produce a layer thickness of between .004” to .006”. For FDM, slice thickness is recommended at .007” to .20” due to its build style. Thicker FDM resolutions are great for large, non-cosmetic parts such as prototypes, because they can be built faster and cheaper.
Wall Thickness
After you decide on your optimal layer resolution, wall thickness enters the equation. Wall thickness is a fundamental design feature that ensures stability, accuracy, and tolerance for any 3D printed part. Thinner walls lead to shorter build times – but make your walls too thin and your part could be flimsy or have less accurate features.
Thin-walled parts built using LS are more likely to warp due to its build style. LS parts are subject to high temperatures and the weight of the powder surrounding the part during the build; LS plastic materials also slightly shrink as the part cools and solidifies. A wall thickness between .40” to .120” is recommended for geometric stability.
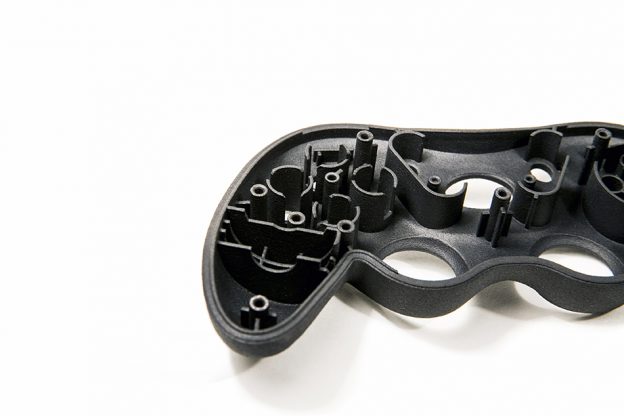
Wall thickness is an important design feature to ensure stability and accuracy, while maintaining a geometries detail.
For FDM, the recommended minimum wall thickness is four times the layer height. For example, if you are designing the minimum FDM layer height at .007”, your minimum wall thickness should be .028” in order to eliminate brittleness in your part. Wall thickness is an important design feature to ensure stability and accuracy, while maintaining a geometries detail.
Build Orientation
Build orientation is another important consideration to keep in mind in this equation for optimal geometric stability. Orientation in 3D Printing refers to how and which direction a part is placed on the 3D printing build platform (X, Y or Z). The part might be oriented at an angle, stand vertically, or be laid flat. Build orientation is a crucial step that affects part quality, especially geometric dimension and tolerance errors, the energy expended, and the extent of the support structures needed all contribute to the overall cost of the part.
Keep in mind that different technologies lead to building parts at different orientations. With FDM, the extruded plastics will be strongest at the tensile mode along the X-Y plane and at its lowest strength in the Z-direction because of the technology’s build style of layers cooling and solidifying while another layer is added on. Building big, flat surfaces horizontally could also affect the accuracy of the part and result in warp due to the large surface area of the part parallel to every new layer of material.
Some build orientations work better for curved or square features, while others result in more visible layer lines that will affect the aesthetics of your final part, and some orientations will deliver more overhangs, resulting in the need for supports.
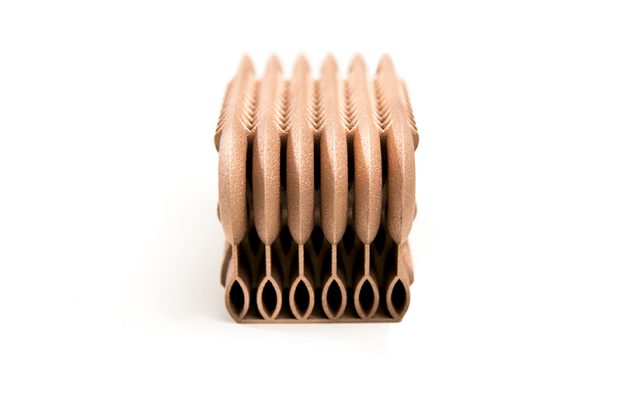
Design balance can pay off, as seen in this complex DMLS heat sink, designed for thermal management applications.
Conclusion
Finding the ideal balance for your design can be challenging even to those with years of experience. If you are new to additive manufacturing, there are a lot resources available. Consider reviewing technology design guides or for a more robust design challenge, Design Services will work with you to optimize your design for additive manufacturing. When your design is ready, if you don’t have access to a 3D printer, let Stratasys Direct Manufacturing make the part for you.
Be the first to post a comment.