The world of 3D printing is constantly evolving and expanding, and one area in which we are seeing a technological renaissance of sorts is the footwear realm. 3D printing technology has now enabled product customization of sneakers, not only with regard to aesthetics but with the aim of physically helping people. Sneakers can now be printed and tailored to a runner’s biometrics or to the individual’s low or high foot arches.
Generally the time-scale of developing a new sneaker product can span over a year, but 3D printing as both a prototyping tool and a manufacturing technique can drastically reduce that timespan. Instead of using expensive steel molds and costly thermoplastic injection molding, with 3D printing sneaker companies can prototype shoes quickly and more affordably. Still, it may be a while before we’re all wearing this kind of futuristic footwear – but more on that later.
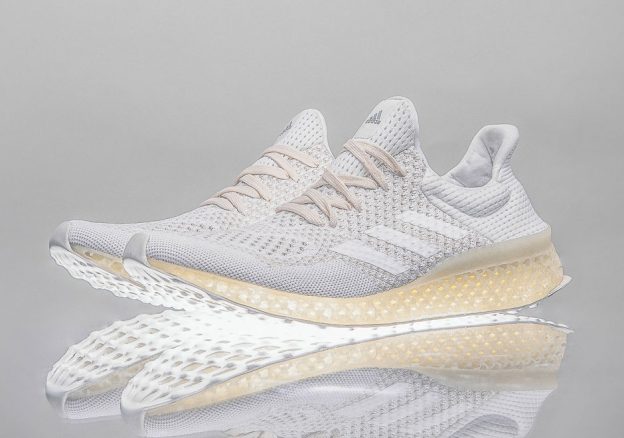
The Adidas Futurecraft 4D is one of the many sneakers developed thanks to 3D printing technology hitting the market recently.
Which Companies in the Sneaker Industry Have Embraced 3D Printing?
Adidas
Adidas is undoubtedly one of the front runners in the 3D sneaker printing race. It’s Futurecraft 4D concept (the company’s first 3D printed shoe) is a running shoe containing midsole, which is customized to the person’s foot “matching exact contours and pressure points,” according to Adidas. The company says they imagine a future where you will be able to run briefly on a treadmill at an Adidas store and walk out with a 3D printed shoe customized to your exact specifications.
Earlier this year, Adidas announced the UltraBOOST Nest, which was designed by architecturally trained designer Nathan Kiatkulpiboone, also known as KXIV. It took inspiration from the Beijing National Stadium used to host the Olympics in 2008. 3D printing is used to create the shoe’s “locking system” of criss-crossing plastic strands.
Adidas has also partnered with Silicon Valley-based tech company Carbon to create Futurecraft 4D’s midsole. It’s the most comfortable shoe sole we’ve ever seen using 3D printing. In fact, Time Magazine has named it as one of the 25 best inventions of 2017.
Futurecraft 4D is Adidas’s first application of the Digital Light Synthesis (a process that uses digital light projection, oxygen-permeable optics and programmable liquid resins to generate high-performance, durable polymeric products), and represents the brand’s step into athlete-data driven design and manufacturing. The liquid plastic outsoles of the shoe can be customized to precisely fit a runner’s foot, a process that would typically take days that Adidas has cut to just hours.
According to Carbon, its “unique programmable resin platform offers unparalleled performance with respect to material durability and elastomeric responsiveness.” Adidas plans to produce 100,000 pairs by end of 2018.
Nike
Nike’s Hyperadapt 1.0 made Back to The Future‘s self-lacing shoes a reality, according to Digital Trends. It produced a 3D-printed shoe built for linear speed and found success with a variation of this process for the company’s Flynit shoes, which involves sending a design file to one person, who then places the file in a knitting machine to make the shoe.
Speaking at the GeekWire Summit in 2015, Nike’s CEO Erick Sprunk proclaimed a future where Nike would sell the digital file of a sneaker design to consumers, who could then print it in their own homes or have them custom made at a retail store.
SOLS
SOLS, is a company that allows people to take pictures of their feet, send them to SOLS via the company’s mobile app, and receive a set of customized insoles within just a few days.
Reebok
Reebok’s Liquid Factory also used 3D printing to make its own intricate and visually stunning designs before the company debuted a completely recyclable and wholly unique footwear line dubbed Cotton + Corn.
Under Armour
Elsewhere, Under Armour is turning to 3D printing to power the next revolution in sneaker technology.
“A lot of competitors talk about it, but we like to get it done. We want to see what the consumer has to say,” said Under Armour vice president of outdoor and training footwear Chris Lindgren to Sports Illustrated.
The company believes the flexibility of a training shoe (vs a running shoe) will appeal to a wider variety of consumers who are looking for a shoe that can take them from the weight bench to the treadmill and back.
When designing the 3D Architech, UA worked with over 80 athletes who tested and provided feedback on the shoes. UA produced an “innumerable” number of shoes that were used in over 120 hours of testing. This scale of prototyping and design would not be possible using the traditional molding process.
UA hopes to refine the 3D-printing process as it gathers feedback from consumers and will use this information to tweak future models. It also plans to expand the process to allow for customization by users who will be able to pick and choose designs as they create their perfect shoe.
Beyond the consumer market, UA hopes to combine scanning technology with 3D printing to build a shoe crafted precisely for an athlete’s foot size and forefoot shape and arch.
The future
The future is all about customization, and 3D printing allows sneaker companies to produce personalized shoes rapidly and with potentially less expense in the long run.
However, while technology may be making our sneakers smarter and trendier, it will be a while before we’re all wearing personalized, 3D designed footwear. This is largely due to under production so far and overpricing for the average sneaker buyer.
The good news? There’s still plenty of hope for the future. Like all new advances worth their salt, the technology in these shoes will start expensive and small scale, gradually becoming cheaper and more mainstream over time.
Be patient.
What’s the difference between Fused Deposition Modeling (FDM) and PolyJet 3D printing technology?
Be the first to post a comment.