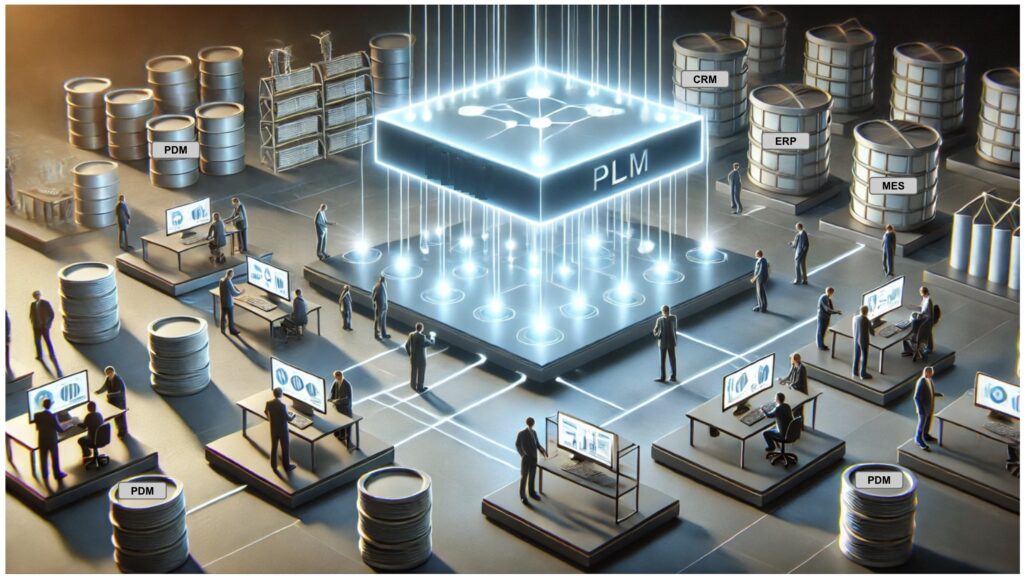
The debate over whether Product Data Management (PDM) and Product Lifecycle Management (PLM) are distinct or intertwined systems has persisted for years. Countless comparisons highlight their differences, yet the boundaries between the two remain blurry. This confusion extends to recommendations for engineering teams and companies.
PDM and PLM – Are They the Same or Different?
Here are few examples of the definitions for PDM and PLM. There are many others. I captured them online here and here. Some companies will try to convince you to buy PLM for a better ROI.
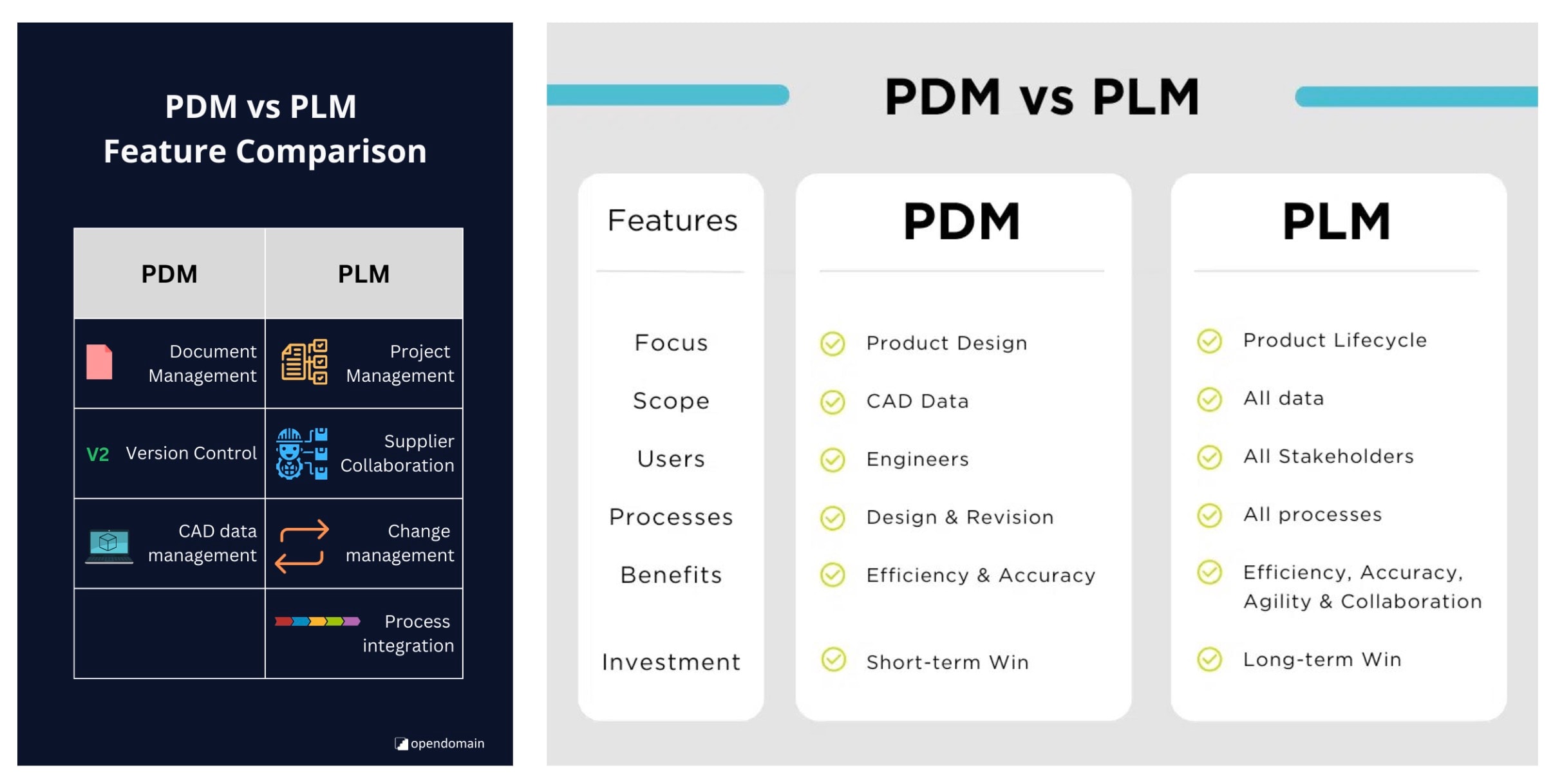
Another perspective is to check how large CAD vendors provide the position. Here is an example from Cadence and from PTC. While Cadence provide a more balanced way of difference that you might consider complementary to many other definitions above.
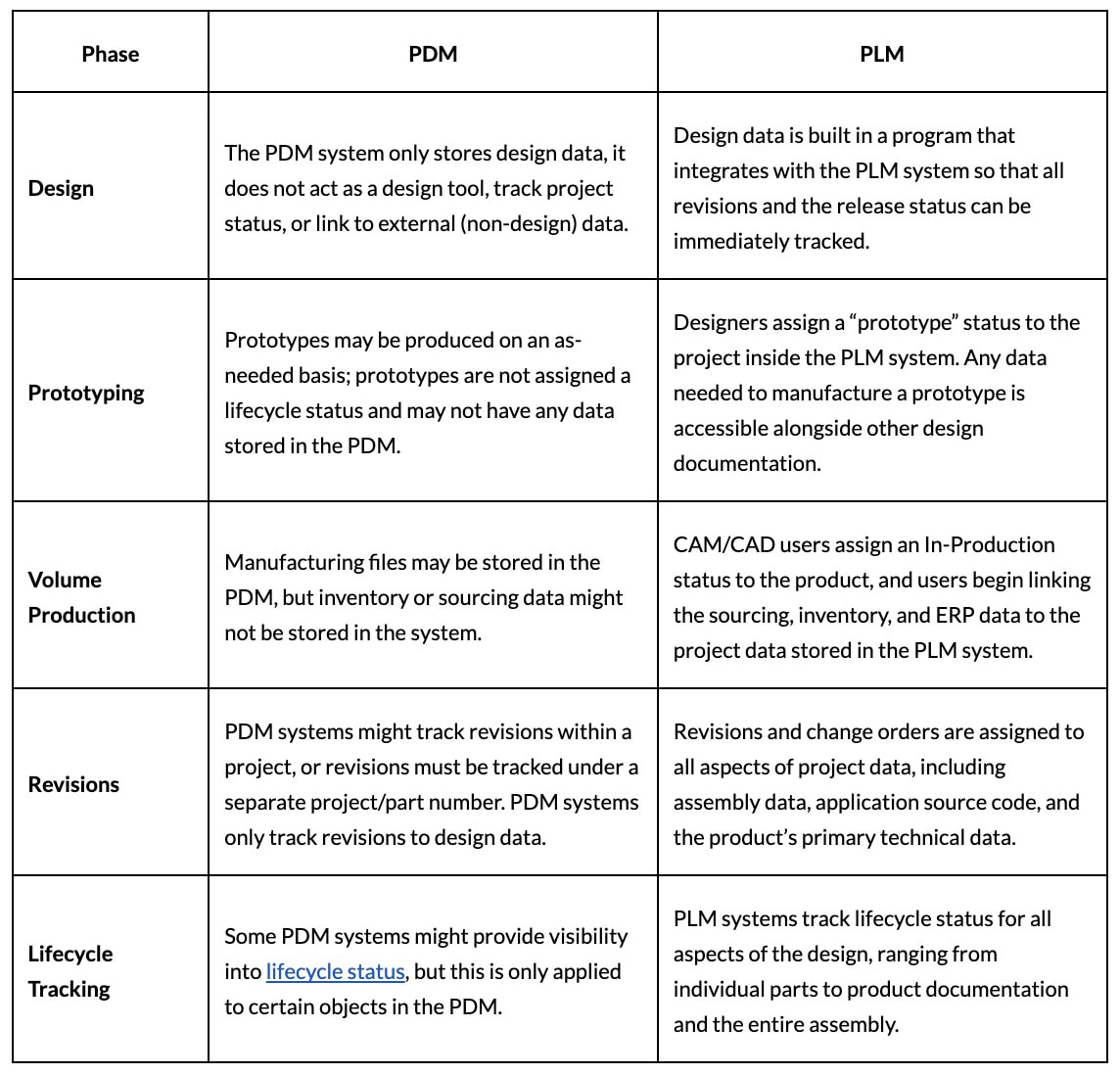
The definition from PTC is a bit different. While the outline mentions a traditional PDM vs PLM separation the conclusion is that PTC Windchill gives you both functions. Here is the passage:
It’s clear that PDM and PLM are two different (if closely related) manufacturing solutions. Choosing one or the other can involve costly tradeoffs either way. But PTC’s Windchill eliminates the need to make a binary choice. Windchill includes PTC’s PDM solution, designed specifically for enterprise PLM. In fact, while available as a stand-alone function, PTC’s PDM is seamlessly integrated into PTC’s powerful and comprehensive Windchill PLM solution. That means Windchill lets businesses start where they are in introducing PDM, and scale up to full PLM functionality as they grow.
So, do we need one or both? The answer becomes even murkier with the reality of modern complex products – comprising mechanical, electrical, electronic, and software components – enter the picture.
For instance, do you require multiple PDM systems for each CAD tool? What if your cloud-based CAD system already includes PDM functions? And what about tools like JIRA—can they suffice as a PLM solution? These questions illustrate the complexity of navigating the PDM and PLM landscape. The challenge lies in building a strategy to determine what system is right for you and when you need it.
History: The Birth of PDM
PDM systems emerged from the need to manage complex CAD files in industries with highly configurable and complex products, such as automotive, aerospace, and heavy machinery. Organizing information, tracking changes, and managing configurations were complex tasks, particularly in industries where complex configurations and long product lifecycle were critical.
Initially, PDM systems were developed as toolkits to manage data and support CAD file management. As CAD adoption surged across industries, the need for effective data management became universal. Over time, PDM functions evolved, expanding their scope to address collaboration and data sharing needs across various sectors.
Does PLM is actually PDM+?
As CAD vendors extended their data management capabilities, PLM emerged as a broader framework. PLM promised to manage “processes beyond PDM,” encompassing areas like engineering workflows, approvals, and lifecycle management. This expansion resonated with industries needing solutions for the growing complexity of product development.
PLM is a PDM+ and what happened when CAD/PLM vendors introduced PLM as a marketing concept. CAD vendors were expanding their data management concepts and PLM was a framework that used to explain “processes beyond PDM”. It was easy to describe and sounded like something that was easy to sell. What helped at this stage is that industry needed simple systems to support CAD file management for massive expansions of CAD packages (eg. AutoCAD, SolidWorks, and many others). Everyone needed “some data management” and PDM systems provided ease of use and simplicity took the niche.
Unfortunately, the word PLM was over used and presented every time when it was the need to speak about “bigger, broader, and more complex functions”. While PDM was straightforward and accessible, PLM positioned itself as the next step for organizations seeking to move beyond file management to process optimization. It was a natural evolution, though it introduced a sense of over complexity and rejection.
PDM vs. PLM: The Divide
The distinction between PDM and PLM wasn’t just about functionality; it was also about pricing and positioning. Vendors used the divide to justify premium pricing for PLM systems by labeling advanced functions as part of PLM while keeping PDM as a simpler, more affordable option. This segmentation became evident in enterprise PLM systems like Windchill and Teamcenter, where PDM functions acted as the foundation, with PLM adding layers of process management.
This divide, however, often created confusion for companies trying to determine what they truly needed and when.
Complex Product Development, Enterprise and TDM Function
As companies adopted multiple CAD tools, often due to organizational or functional silos, managing multi-CAD environments became a challenge. This led to the rise of another term TDM (Team Data Management) as an intermediary layer, bridging CAD systems and enterprise PLM solutions. In some industries and geos, enterprise PLM was bundled with ERP functions and used ERP position for unified data layer.
In this position, TDM function simplified integration by isolating CAD/PDM functions, allowing enterprises to manage CAD data without overhauling their entire PLM infrastructure. This approach provided a practical solution for managing diverse CAD environments, though it also highlighted the limitations of traditional PDM/PLM divides.
The Complexity of Products and Future PDM/PLM Trajectory
Modern products are significantly more complex than those of the past, blending mechanical, electronic, and software components. This complexity raises questions about the systems needed to manage such products effectively. Smaller teams now face challenges similar to those that once plagued large enterprises, requiring advanced data management solutions to keep pace.
Meanwhile, enterprises are grappling with even greater complexity, such as managing Engineer-to-Order (ETO) and Configure-to-Order (CTO) processes, while connecting design to manufacturing, procurement, and support. What was once a straightforward need to manage MCAD files has grown into a multifaceted challenge involving configurations, electronics, software, and services.
PDM “murder” by CAD vendors and Way Forward
CAD vendors disrupted the standalone PDM market by acquiring PDM providers and embedding their functionality into CAD systems. This strategic move eliminated the need for independent PDM tools, as CAD solutions started offering data management features like revisions and collaboration directly within their platforms.
With the rise of cloud CAD systems, such as Onshape and Fusion 360, this trend accelerated. Cloud CAD tools were built with integrated PDM capabilities as standard, making standalone PDM solutions largely obsolete. For companies, it simplified workflows and reduced costs. For standalone PDM vendors, it marked the end of their dominance.
While integrated PDM in CAD systems simplified processes, it came with limitations. Users were tied to a single CAD ecosystem, limiting flexibility. Reduced Innovation: Fewer independent PDM providers led to slower advancements in the field. Narrow Focus: CAD-centric PDM doesn’t address broader lifecycle needs like manufacturing and supply chain integration.
As products grow more complex, the limitations of CAD-centric PDM are increasingly clear. Modern solutions like OpenBOM aim to bridge the gaps by offering flexible, open, and comprehensive data management across disciplines. The future lies in balancing integrated PDM convenience with robust, unified lifecycle management to meet the challenges of today’s intricate product development.
Organizing the Engineering Process and Product Lifecycle
The growing complexity of products and processes underscores the need for a unified data management layer. This layer must provide a complete digital representation of product information, align design teams, and coordinate changes across disciplines. Traditional PDM systems embedded in CAD tools cannot meet these needs alone.
Instead, what’s required is a comprehensive approach—a “digital product information layer” that facilitates collaboration, manages revisions and changes, and connects design with manufacturing and procurement. This layer may evolve beyond PLM as we know it today, but its role in enabling engineering and manufacturing collaboration is indisputable.
Here is just one example of PLM layer offered in the presentation done by Martin Eigner during SAP Innovation day a few weeks ago.
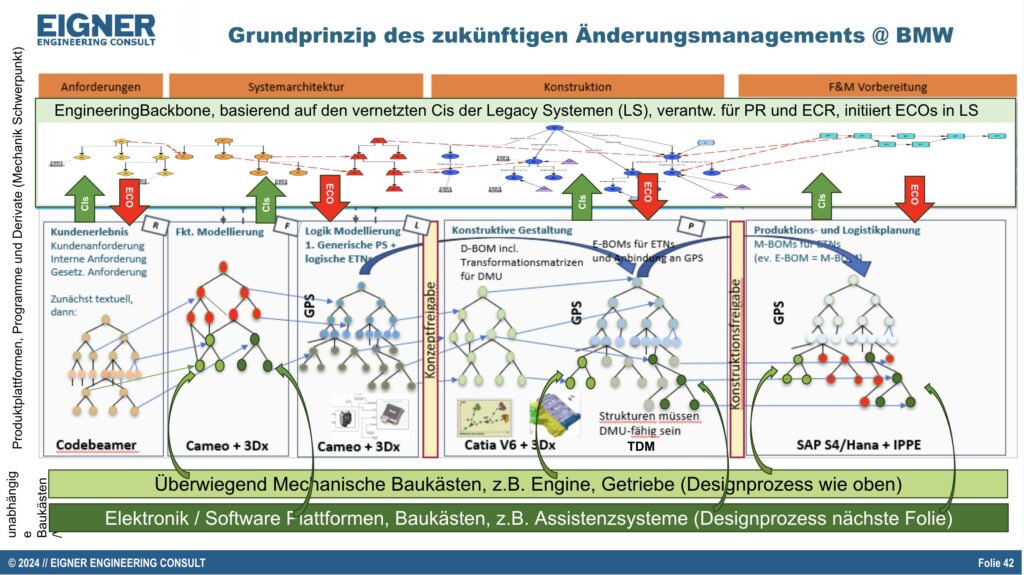
Here is another example of PLM layer organized by OpenBOM Product Knowledge Graph called “digital BOM”.
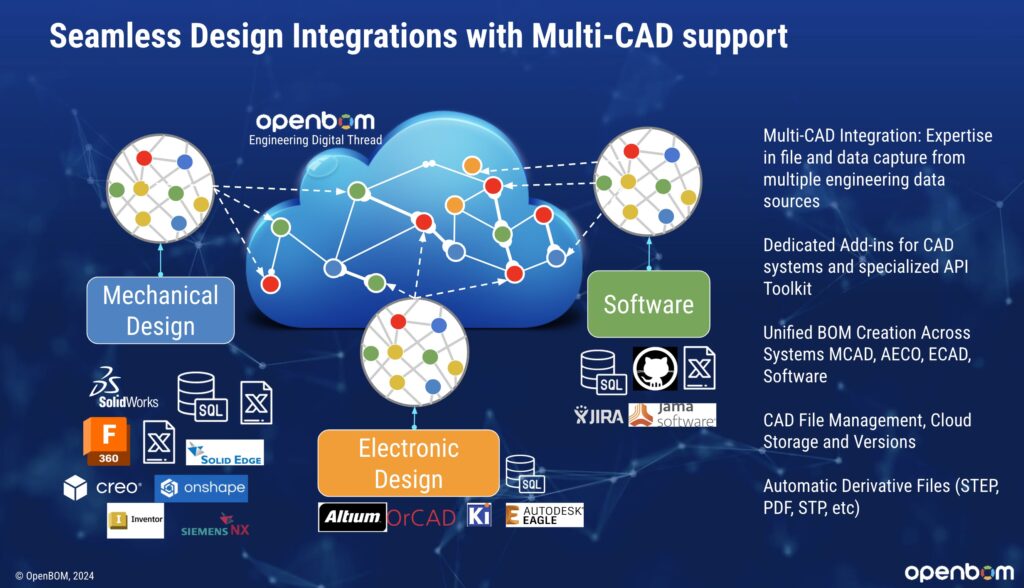
One more option of organizing information in layers from ProSTEP demonstrating two layers for TDM (Team Data Management) focused on specific CAD and a holistic PLM layer using OSLC model.
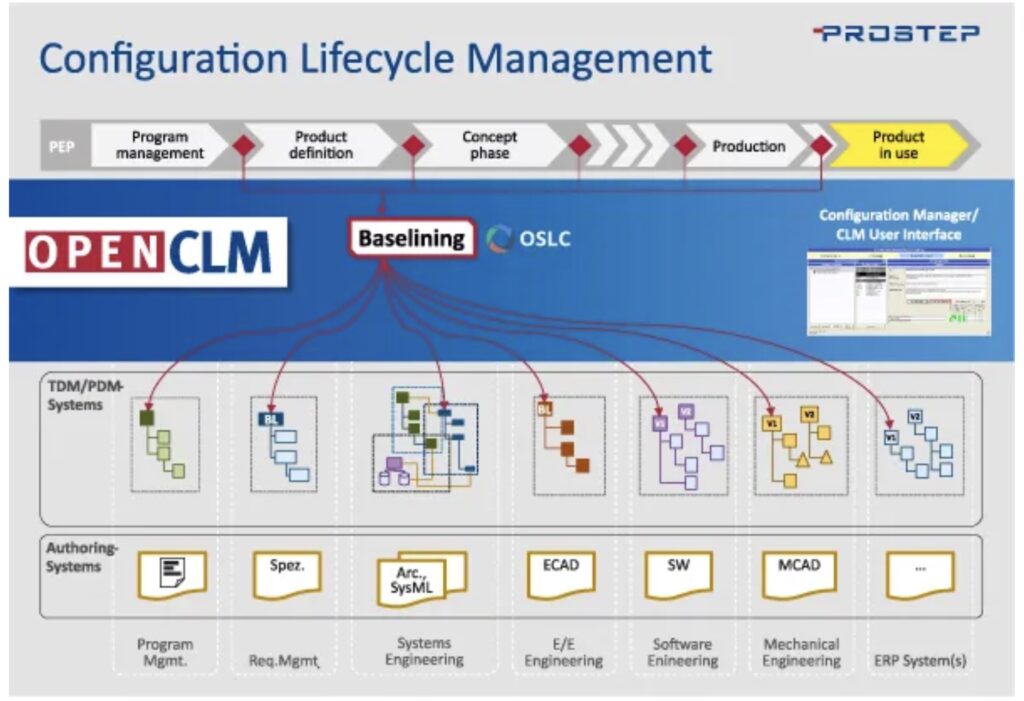
What is my conclusion?
The future of PDM and PLM lies in their convergence and evolution. PDM functions are increasingly integrated into CAD systems, reflecting their close relationship with design processes. At the same time, the growing complexity of products demands a broader, more integrated approach to data management—one capable of consolidating mechanical, electronic, and software components while supporting manufacturing and procurement.
Future PLM software will require a “new PLM” model, or whatever term it may be given, that will serve as a central hub to support product development process, production process, service lifecycle management and connectivity to enterprise resource planning. There is need for a new product data layer for managing product data, engineering management, ensuring traceability, and enabling collaboration across the product lifecycle. As organizations navigate this transformation, the key will be balancing simplicity and scalability to meet their unique needs. Just my thoughts…
Best, Oleg
Disclaimer: I’m the co-founder and CEO of OpenBOM, a digital-thread platform providing cloud-native PDM, PLM, and ERP capabilities. With extensive experience in federated CAD-PDM and PLM architecture, I’m advocates for agile, open product models and cloud technologies in manufacturing. My opinion can be unintentionally biased.
The post PDM vs PLM: Current Status Quo, Challenges, and Future Development appeared first on Beyond PLM (Product Lifecycle Management) Blog.
Be the first to post a comment.