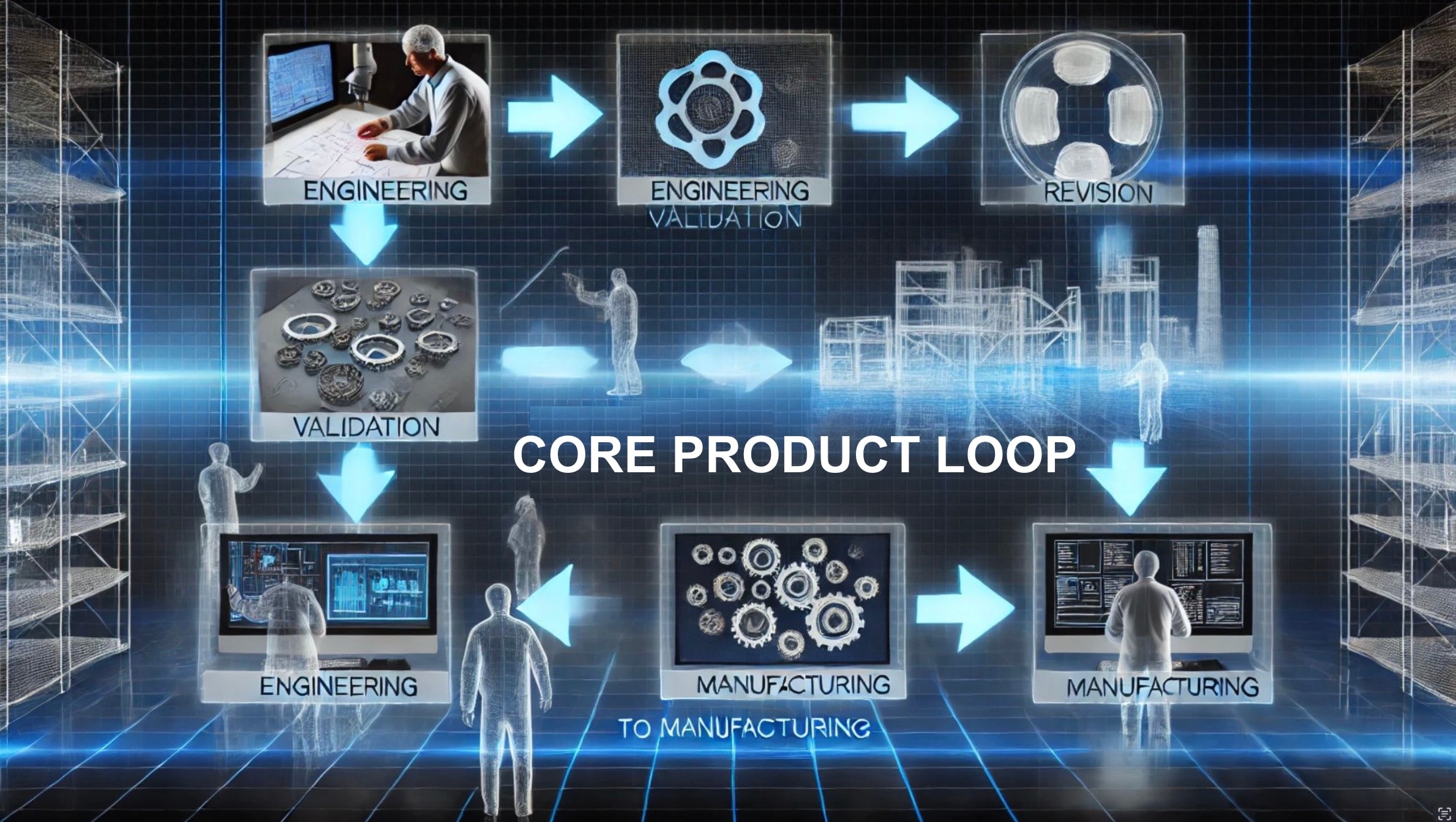
Digital transformation is no longer just a buzzword—it’s a reality changing the way manufacturing companies work. Engineering teams and manufacturing businesses are allocating more resources than ever to explore and implement digital technologies that streamline operations, improve productivity, and leverage the vast amounts of data at their disposal. A recent study by EY shows that 68% of CEOs from leading industrial product companies are increasing their digital and technology investments. However, while the intent to embrace digital transformation is clear, the path to achieving it is not simple and many companies are struggling in this process.
The Challenge: Data Management
Despite the growing investments, one major roadblock remains: data. In many manufacturing companies, data management is still rooted in document-based processes. These processes include handling CAD files, their derivatives (such as STEP, PDF, and DXF), and countless spreadsheets, primarily in Excel. Although Product Lifecycle Management (PLM) vendors promise to move companies away from these static, document-centric approaches toward dynamic, structured digital data, the transition has been anything but smooth.
PLM systems aim to create a single source of truth, where data is continuously synchronized and updated. In theory, this approach reduces the risk of outdated or inaccurate information, improving accessibility and overall operational efficiency. However, despite this promise, the reality is less optimistic. According to CIMdata research, only 17% of companies claim they cannot operate without their PLM systems, while 37% view it merely as an engineering tool, and 27% find it too costly.
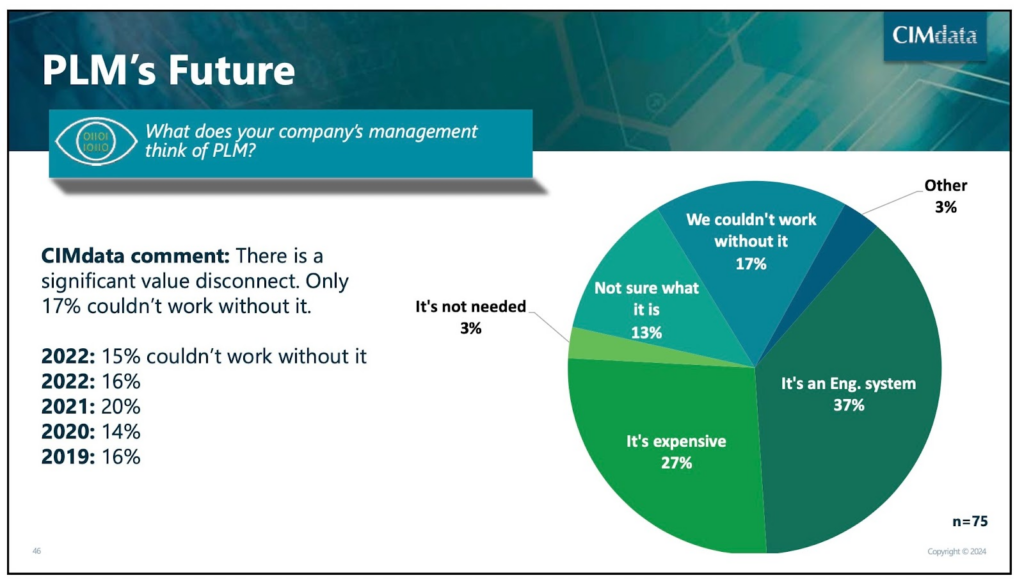
What’s the Right Way Forward?
Many companies are torn between taking no action—continuing with outdated processes—and attempting to overhaul their entire system overnight. Neither of these strategies is ideal. Businesses that refuse to modernize will inevitably fall behind, while those attempting drastic, overnight changes often face disruptions that can harm operations.
Is IT to Blame?
Historically, IT departments have been the driving force behind implementing PLM systems. Their focus has been on organizing information, managing documents, and setting up databases to serve the specific needs of various departments. While IT laid the foundation, “grey IT”—local departmental workarounds—began to emerge as individual teams sought their own solutions for managing information. As a result, CAD/PDM and eventually PLM became siloed within engineering departments. Meanwhile, ERP and CRM systems successfully pitched their value to CIOs, solidifying their dominance in enterprise systems due to their broader business reach.
The problem with most PLM implementations lies in attempting to replicate existing, document-centric processes in a new digital format. This “lift and shift” strategy rarely works well, leaving businesses struggling to realize the full benefits of PLM.
Start From the Business
Many industry experts suggest that companies should begin by focusing on business needs rather than technology. While this approach is sound, the problems aren’t purely business-related. The current landscape of PLM software—along with how companies implement it—presents its own set of challenges.
5 Key Problems in PLM
In a previous article, I outlined five key problems that I can see in the PLM technology, products and implementation these days. Here’s a quick recap:
- Complexity of User Experience: PLM systems typically have overly complex interfaces, making adoption and daily use difficult. While engineers are sort of ok, the love for PLM is dropping down when you move outside of engineering departments.
- Lack of Flexibility: PLM systems often fail to adapt to the specific needs of a company, forcing businesses to adjust their workflows to fit the software. Flexibility is important, but rigid implementation requirements are famous in PLM environments.
- Outdated Data Management: Most of mainstream PLM systems rely on 20-30 years old data management technologies when SQL databases were the only way to manage data. Outdated data models and legacy implementations struggle to scale with the interconnected nature of modern manufacturing companies working and connected together.
- Poor Integration: PLM systems frequently fail to integrate smoothly with other enterprise systems, leading to information silos. Although PLM systems and vendors made a significant improvement in openness and APIs, the integrations are still complex.
- High Total Cost of Ownership (TCO): The costs associated with implementing and maintaining PLM systems can be prohibitively high for many companies. 27% of people answered to CIMdata research in 2023 stated that PLM is too expensive.
Where to Start? Build Core Product Loops
One crucial step toward successful digital transformation in PLM is to build core product loops. But what exactly is a core product loop? Simply put, it’s the fundamental process that defines the value a product brings to its users. For example, the core product loop for a car isn’t the car itself but the convenience and transportation it provides.
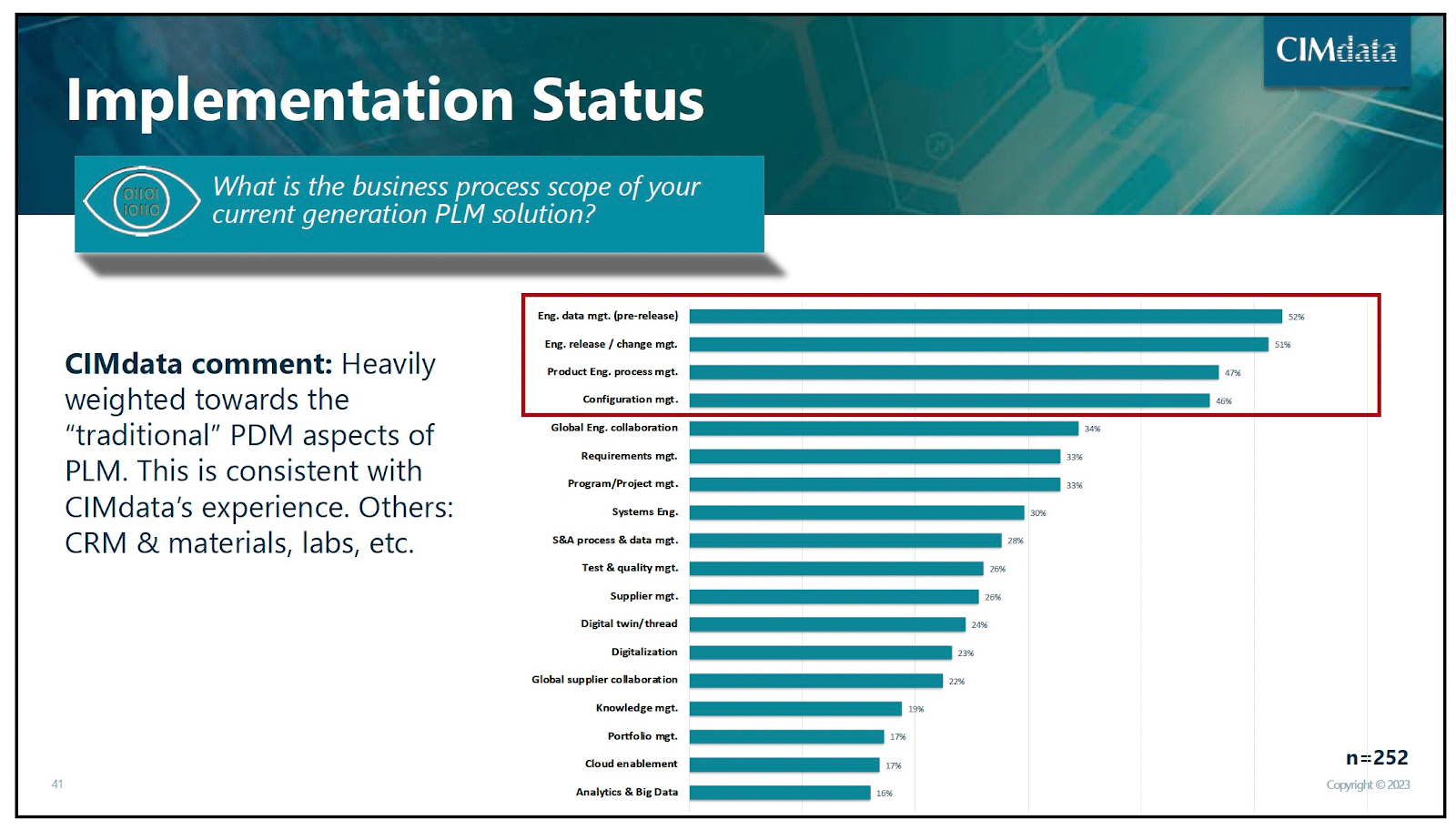
In the PLM context, the concept of a core product loop is often overlooked. Many PLM implementations begin with a broad, strategic framework. Although, the strategy of the implementation might be good, these applications lacks tangible connections to the specific processes users rely on. This is why PLM adoption often struggles, as shown in adoption diagrams where PLM is primarily utilized in clearly defined processes like engineering data management or change management.
How to Build Core Product Loops in PLM?
To drive adoption and realize the true value of PLM, companies need to focus on core product loops—specific processes that support the business. Examples of such core product loops could include New Product Development (NPD), change management, or design reviews, all of which are concrete examples of product loops. The list of core product loops can be long and finding a right one is an important element of PLM software implementation and adoption.
Modern SaaS tools, with their flexible, easy-to-implement nature, are particularly well-suited to support these loops. By focusing on solving specific problems within these loops, businesses can drive adoption more effectively than by attempting to overhaul their entire PLM infrastructure at once.
What is my conclusion?
Successful digital transformation in PLM starts with redefining processes and moving from a document-based approach to one driven by data. To achieve this, businesses need to focus on organizing their core product loops and then applying the right tools to “transform” these loops. Modern, flexible SaaS tools will play a crucial role in this transformation, offering the adaptability and scalability that traditional PLM systems lack. By focusing on specific, repeatable problems, businesses can create a more agile, effective digital future.
Just my thoughts…
Best, Oleg
Disclaimer: I’m the co-founder and CEO of OpenBOM, a digital-thread platform providing cloud-native PDM, PLM, and ERP capabilities. With extensive experience in federated CAD-PDM and PLM architecture, I’m advocates for agile, open product models and cloud technologies in manufacturing. My opinion can be unintentionally biased.
The post Can Effective Core Product Loops Simplify Your PLM Digital Transformation? appeared first on Beyond PLM (Product Lifecycle Management) Blog.
Be the first to post a comment.