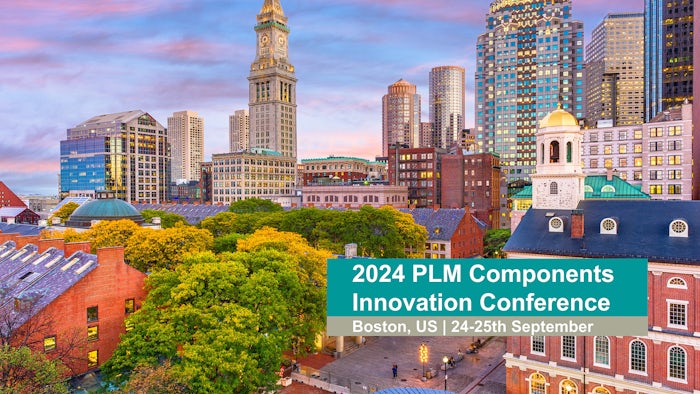
This week, I had the opportunity to attend the Siemens PLM Component Conference in Boston. It was a a great opportunity to learn from Siemens and other companies attending the event that use Siemens PLM components, shared their experiences, insights, and ongoing developments in the computer aided design (CAD) and product lifecycle management (PLM) space. How these components will impact the future of product development processes and PLM software.
Are we going to see future when a technology company in CAD/PLM is going to enable PLM solutions and PLM systems from other companies similar how Siemens PLM components do it for CAD businesses. How design data and product data can become an enabler to use shared components by global manufacturers and optimize the production process. Some answers to these questions are obvious and Siemens PLM components usage confirm that. But some of others are in the future of products lifecycle tool development and future of innovative design of CAD and PLM businesses.
Below are some key takeaways and my reflections on the discussions held during the event.
What Are Siemens PLM Components?
Siemens PLM components are the foundational technologies that drive some of the most widely used engineering and manufacturing software tools. These include Parasolid, D-Cubed, JT, Kineo, PLM Vis Web and more, as well as our OEM offerings, such as Solid Edge and FEMAP OEM versions. During the opening remarks, Tony Hemmelgarn, President and Chief Executive Officer of Siemens Industrial Software highlighted the critical role these components play in supporting industry-wide applications across CAD, PLM, and other tools.
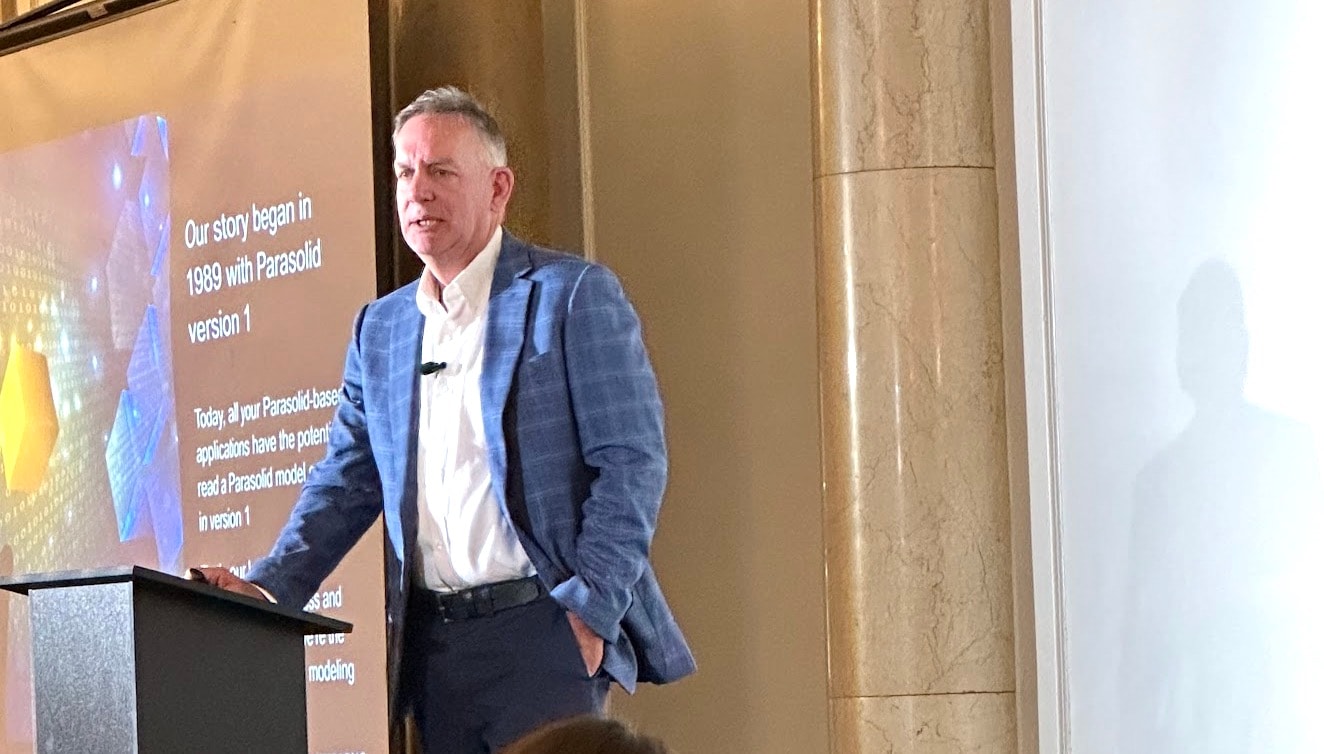
Parasolid, for instance, is the geometric modeling kernel used in numerous CAD systems, offering precision and robustness in handling 3D designs. D-Cube provides constraint solving technology for parametric modeling, while JT facilitates lightweight data exchange for visualization and interoperability across different platforms.
Here are some interesting data points.
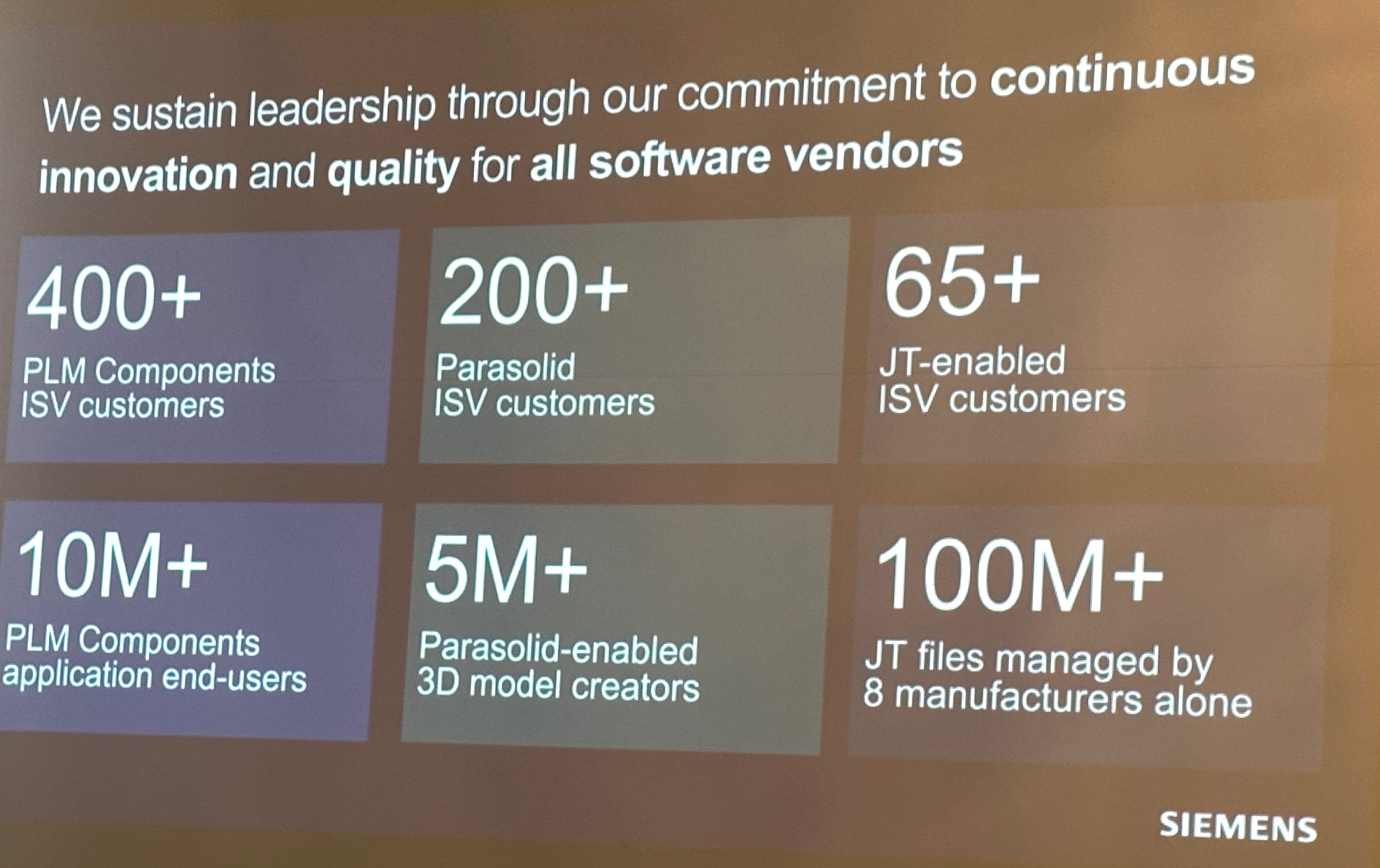
These components are used in a wide range of industry software.
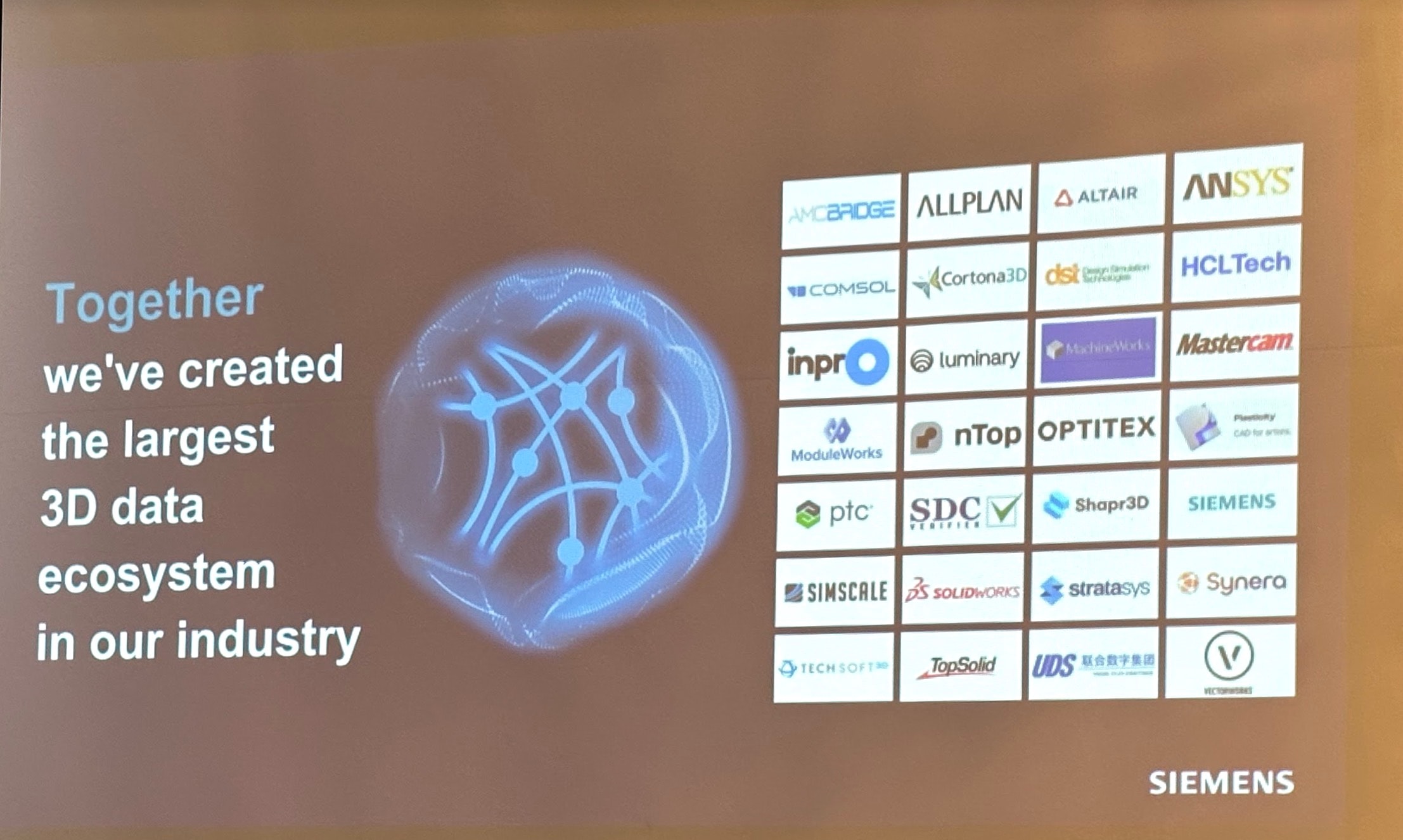
This is a landscape of the components.
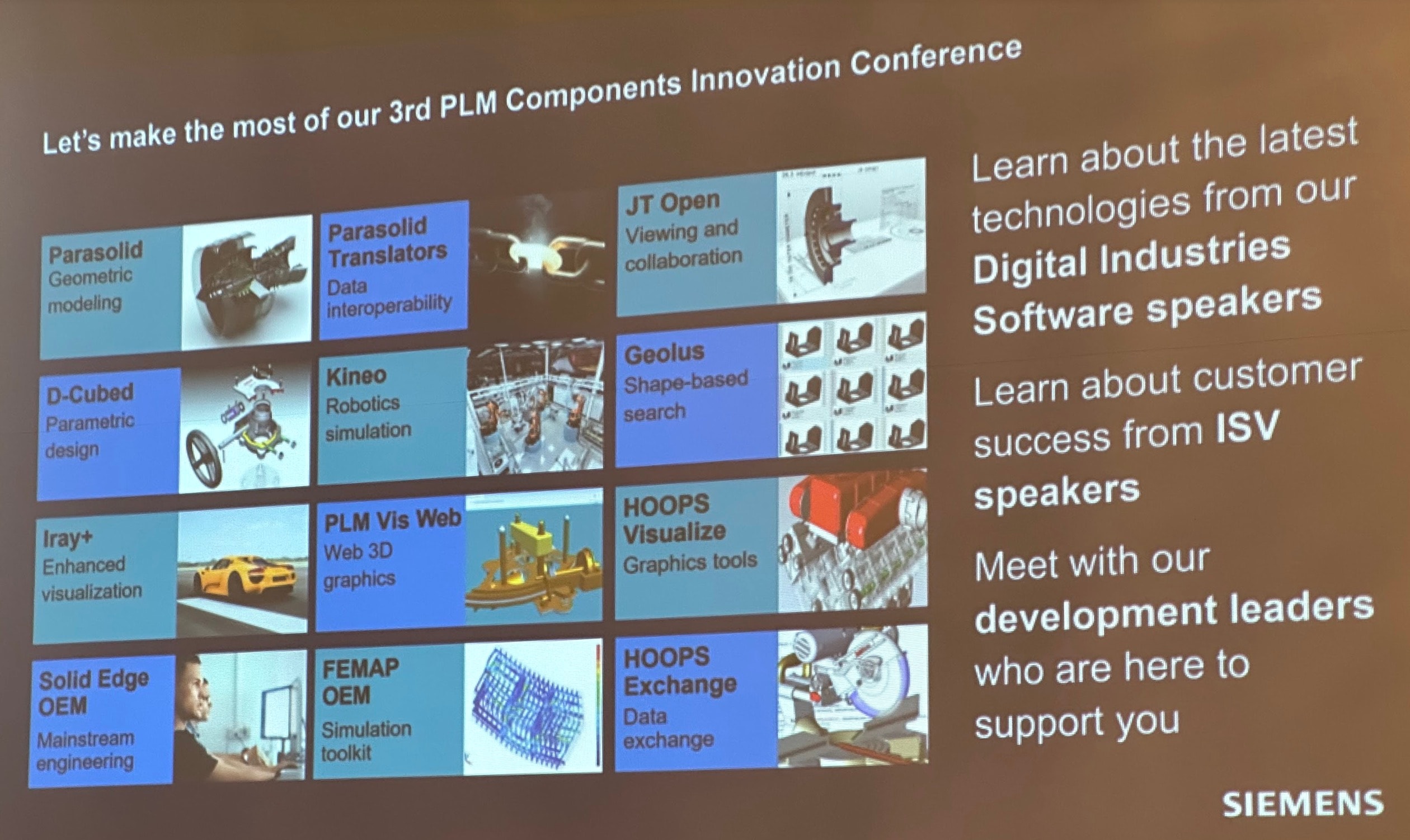
Industry Perspectives
Tom Gill Principal Consultant and Practice Manager, PLM Enterprise Value & Integration of CIMdata shared industry perspective on PLM technology development. He also presented a few interesting data point about usage of Siemens PLM components in the market and CAD space. Check this out.
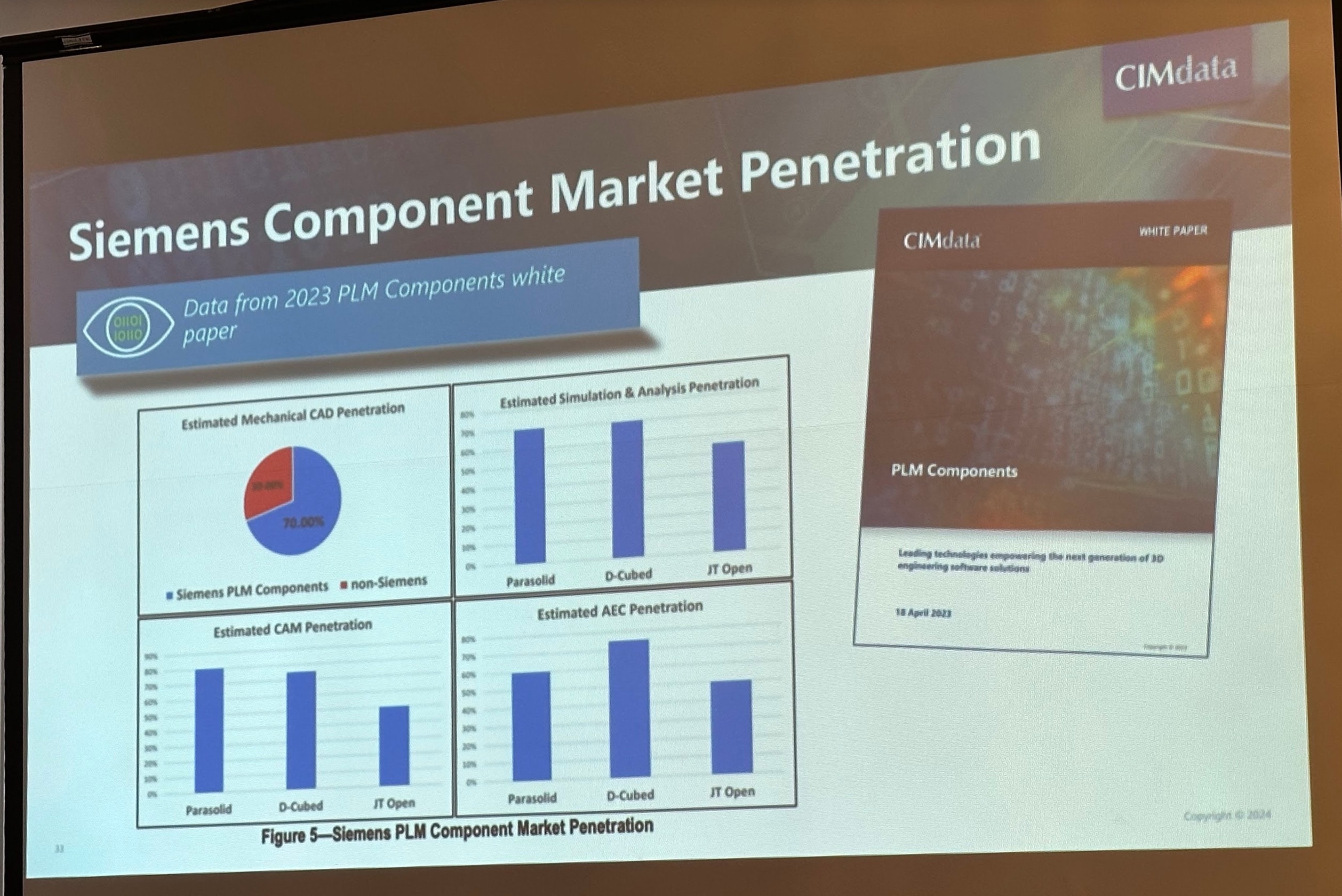
According to Tom, a large percentage of CAD software in use today relies on Siemens technology, showcasing the far-reaching impact of these components on the industry. It triggers an interesting question about what will be the future trend in components usage.
CAD, CAM, CAE Companies Sharing Experiences
Several prominent companies took to the stage to share their experiences using Siemens components, with a focus on Parasolid for CAD development. Companies like PTC Onshape, nTop, Shapr3D, and SimScale offered insights into how they leverage these technologies to build next-generation design tools. Each of these companies illustrated how Siemens components serve as a reliable backbone, allowing them to innovate rapidly and deliver tailored user experiences. Here are a few interesting notes and slides I captured.
PTC Onshape shared how they build a cloud-native architecture with Parasolid geometric modeling kernel foundation (it is the second CAD company co-founded by Jon Hirschtick using Parasolid. The first was Solidworks)
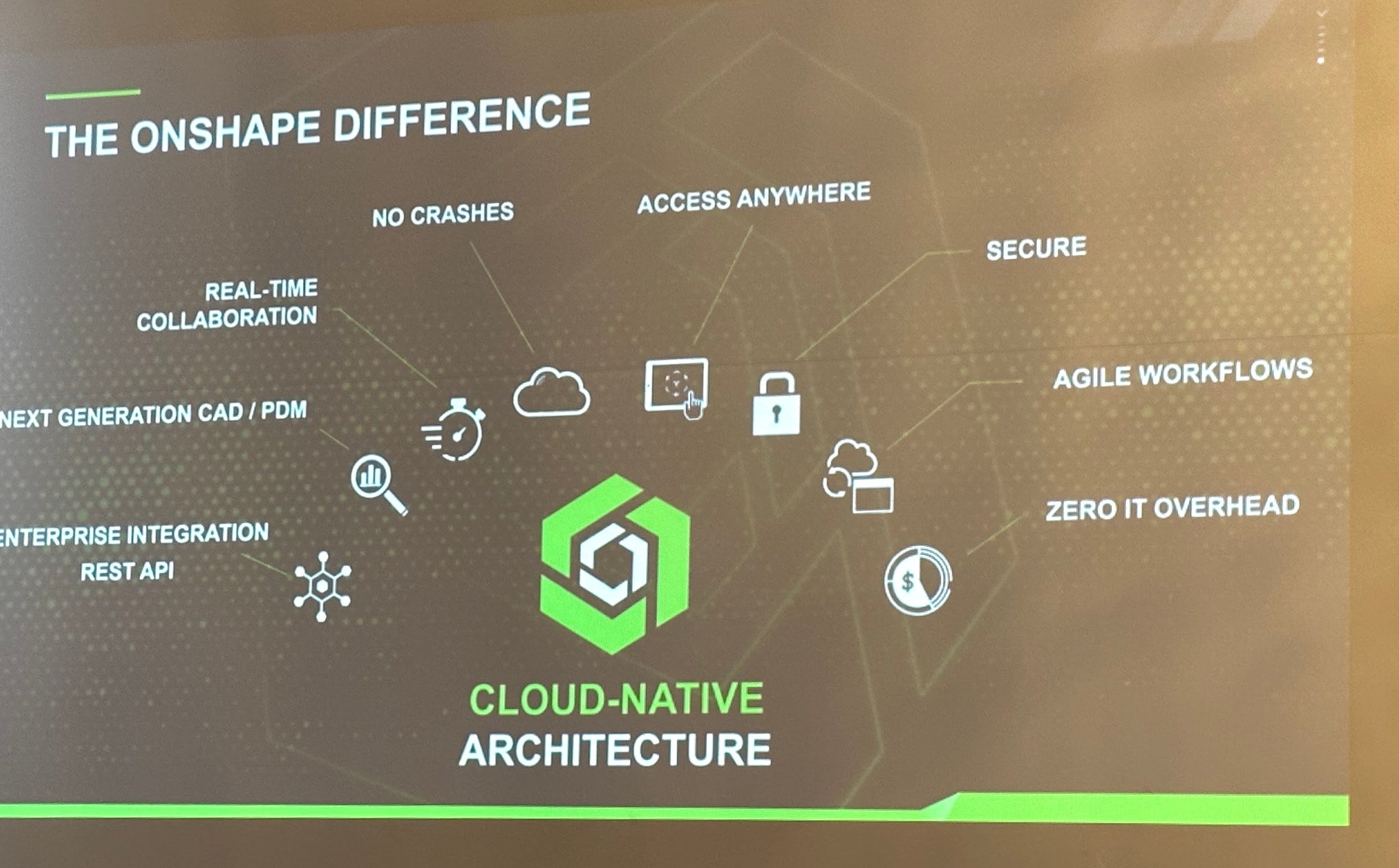
SimScale is another cloud-native product which is also using Parasolid.
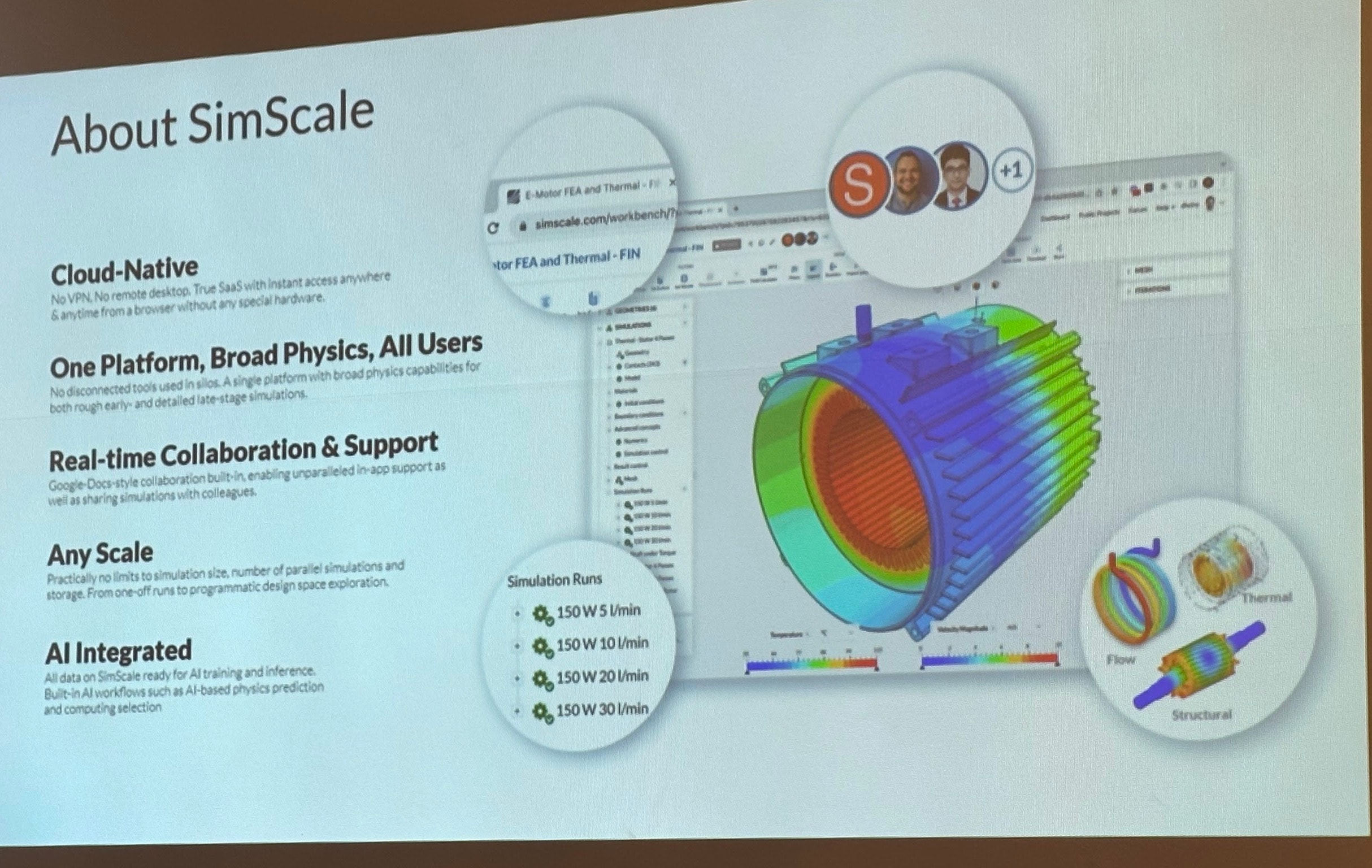
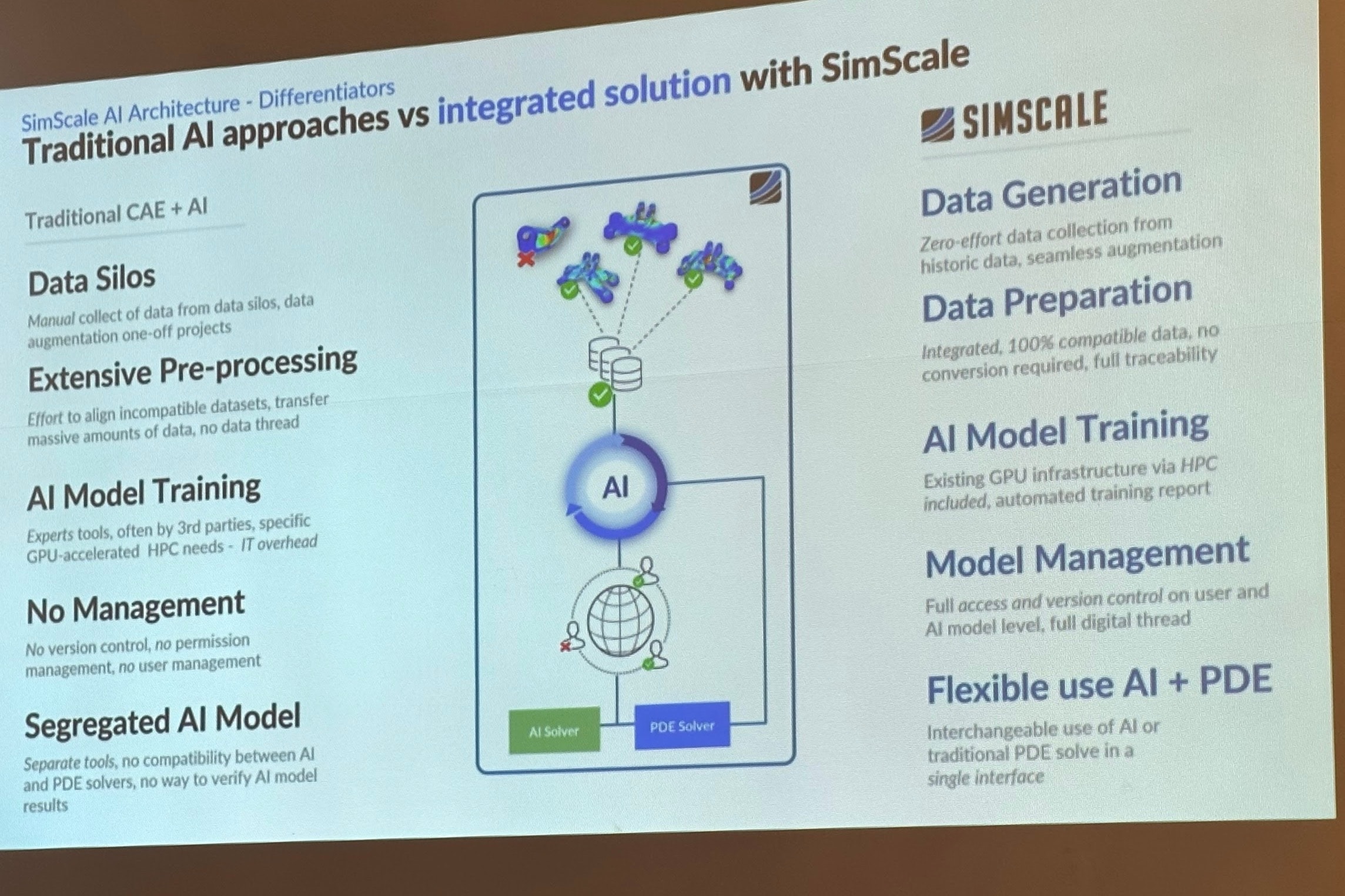
A very interesting perspective on cloud innovation for CAD and enterprise was presented by István Csanády, founder and CEO of Shapr3D. Started as a CAD system for mobile devices, Shapr3D moved to Parasolid and is continue to develop Shapr3D to democratize access to 3D information for enterprises.
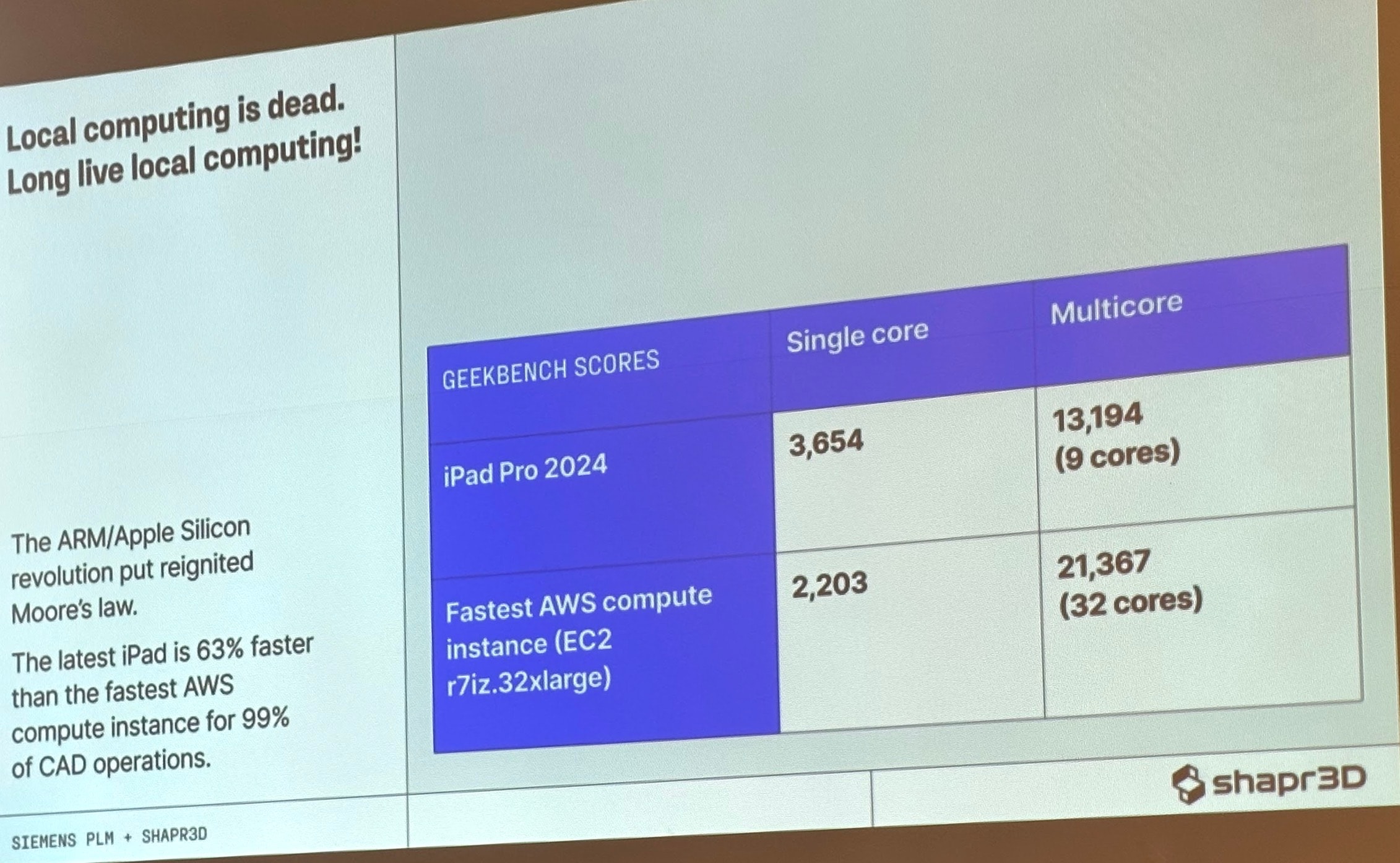
The idea of how to leverage the power of local computing in the cloud-era is a notable innovation that worth paying attention.
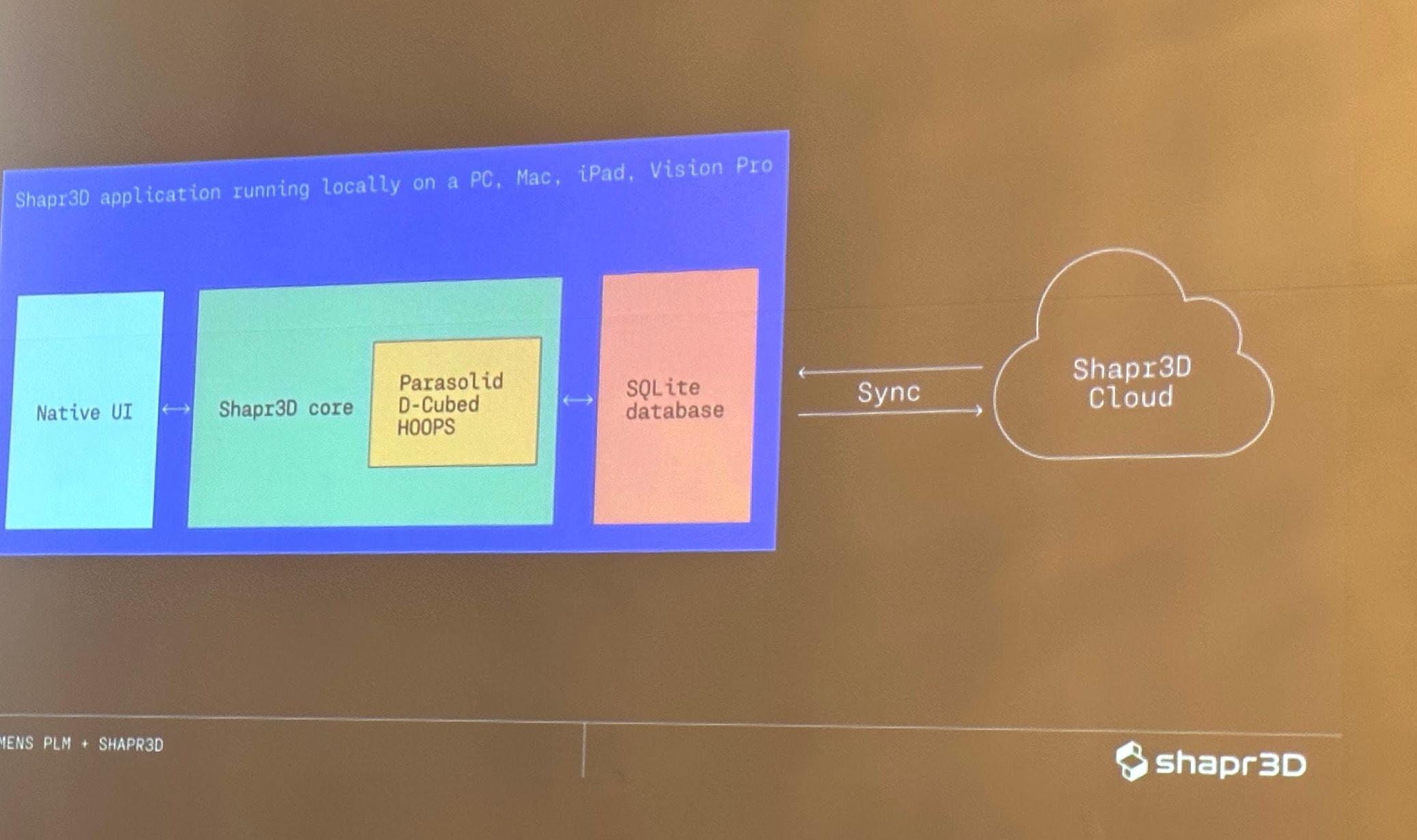
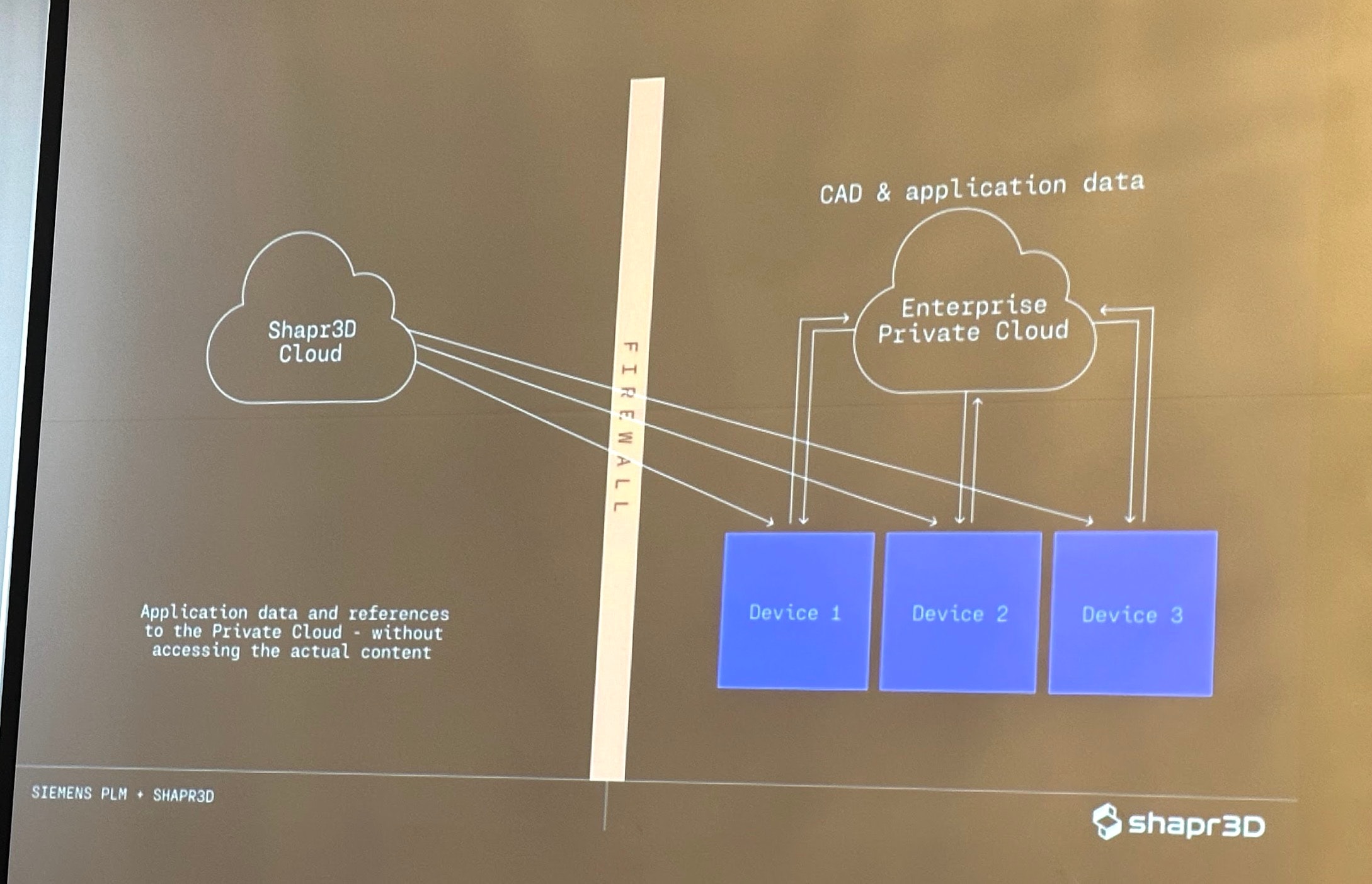
A great panel of Future of CAD moderated by Monica Schnitger of Schnitger Corp a leading analyst for CAD, PLM, and AEC businesses.
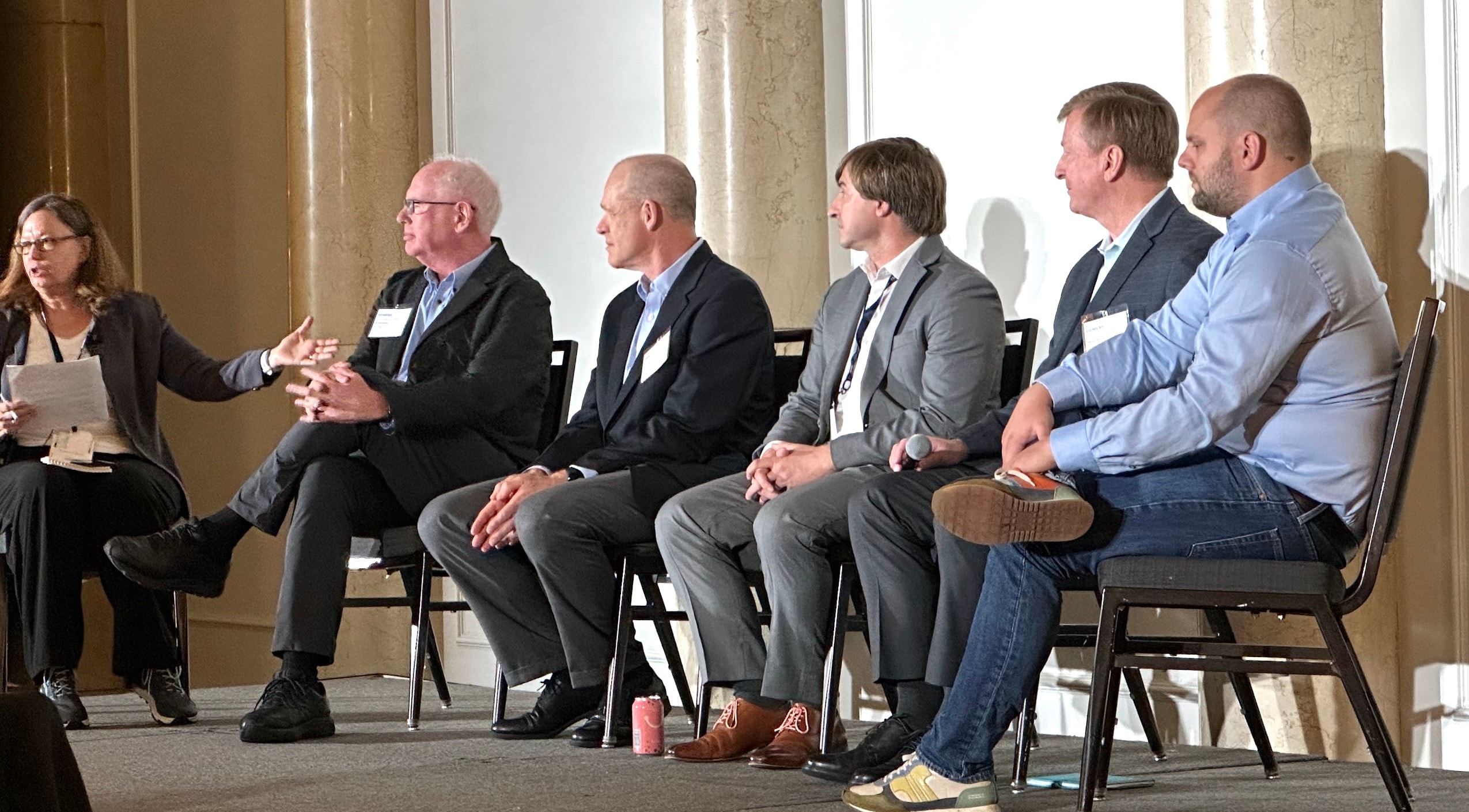
Here are a few notes from the discussion.
Cloud native, speed to develop is the desire of all users. To provide an open library of design can be a strong driver for the future of AI. Community can take an advantage of the future AI tools. Boomers retire and a question of how to preserve the knowledge is becoming critical. Solving customer problems is critical. While AI at the peak of hypecycle, solving customer problems and enterprise adoption are the big deal. Not everyone can get an access to the CAD and other related data in the enterprise UX is a key in geometry and diverse UX experience matter. It is not about geometry, but about user experience. Seamless CAD and data management will become a possible innovation in the future of CAD. Shared components help to support standard development. Shared components will help to develop a better digital thread. But the question of how to develop shared components is not a simple one. Interconnected EBOM/MBOM and other BOM beyond just CAD and geometry will create a foundation for digital thread and connected processes. Agility is important. Large companies want to have an agility and speed of small companies.
Shared Components and Industry Development
One of the recurring themes during the conference was interoperability—a topic that has long been discussed in the CAD and PLM industries. Siemens demonstrated how its portfolio of shared components enables seamless data exchange and collaboration across various platforms. These shared components act as common building blocks, fostering an ecosystem where companies can create robust, interoperable applications while benefiting from the core technological elements Siemens provides.
By utilizing these shared components, software developers are able to focus on innovating within their specific domains without having to reinvent the wheel for core functionality. This approach not only accelerates development but also ensures that different tools can work harmoniously in complex workflows, addressing one of the key challenges of modern engineering environments.
Does the Use of Standard Components Lead to the Commoditization of CAD Software?
One of the opinions circulating in the industry is whether the widespread use of standard components like Parasolid and JT could lead to the commoditization of CAD software. While it’s a valid question, I believe that the true challenge in engineering software lies in its complexity and the diversity of use cases. The “one size fits all” model doesn’t work in this field. Certain use cases require highly specialized tools, while others demand simplicity and specific user experiences.
The fact is, engineering software needs to accommodate a vast array of industries and applications. Therefore, rather than commoditizing the market, shared components actually enable differentiation. By standardizing the foundational technologies, developers can focus on building unique, tailored solutions that cater to specific verticals, user preferences, and workflows. It’s about enhancing the user experience rather than diluting it.
What is my conclusion?
Can standardization become an enabler for CAD innovation? In my view, the use of standardized components is not a threat to innovation; instead, it’s an enabler. These shared technologies provide a reliable, proven foundation that allows companies to innovate in the CAD and PLM space. They empower developers to focus on delivering unique digital experiences that cater to diverse industries, from automotive and aerospace to consumer products and industrial design. By building on these components, companies can not only ensure interoperability but also drive the development of next-generation tools that address the ever-evolving needs of engineers and manufacturers.Standardization, when done right, can be a powerful catalyst for innovation.
However, I expect the future PLM innovation will come in the development of shared services that can be re-used online and deliver a reliable and open environment to support companies workflows. Just my thoughts…
Best, Oleg
Disclaimer: I’m the co-founder and CEO of OpenBOM, a digital-thread platform providing cloud-native PDM, PLM, and ERP capabilities. With extensive experience in federated CAD-PDM and PLM architecture, I’m advocates for agile, open product models and cloud technologies in manufacturing. My opinion can be unintentionally biased.
The post CAD Innovation and Components Standardization: My Takeaways From the Siemens PLM Component Conference in Boston appeared first on Beyond PLM (Product Lifecycle Management) Blog.
Be the first to post a comment.