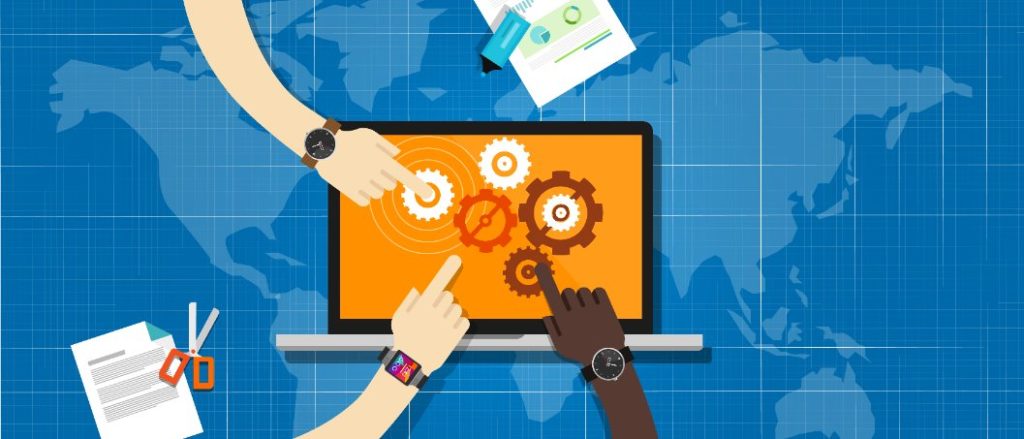
The level of integration in the manufacturing industry is growing. The last decade of advanced manufacturing development demonstrated that setting enterprise systems such as PLM, ERP, MES, and related data and process management for a single company is important but not sufficient to create robust manufacturing processes. Supply chain management plays a key role and quickly becoming an important enabler to connect the dots together. The ability to manage data access multiple companies for design collaboration, engineering, and supply chain management planning is important.
Is Cloud A Magic To To Solve PLM for Supply Chain?
Cloud often comes as a mafic word that is supposed to solve all problems of PLM related to collaboration across multiple departments, companies, and supply chain management. Supply Chain Brain article – Making PLM work in the cloud speaks about the complexity of cloud PLM implementations. Taking existing PLM to the cloud can be very expensive. There is a real danger in taking “lift and shift” approaches by transferring existing PLM architectures to the cloud. Here is an important passage:
…we’re seeing many that have invested in PLM cloud capabilities leaving value unrealized. For example, cost reductions are lower than expected, the migration takes too long and becomes expensive, or critical capabilities aren’t delivered any faster than before. A typical issue companies run into is they design a PLM-on-cloud architecture that it’s more expensive than the current on-premise setup, which leads to inaction. Or a company is unable to deliver performance and security key performance indicators for its PLM cloud capabilities, which leaves business stakeholders dissatisfied.
It’s important to do away with the assumptions and models of the on-premises world; the cloud is something completely different. An attempt to simply “lift and shift” on-premise PLM applications to the cloud and run them as before won’t deliver the breakthrough value you’re looking for. First, you must rationalize and modernize the PLM environment to prepare it for a cloud-native future. Simultaneously, you should look to break down barriers between I.T. and the business. and build a business case that meets the needs of both stakeholders.
Supply Chain Use Cases and Challenges
Jos Voskuil’s article PLM and Supply Chain is a good starting point for learning about various approaches used to solve supply chain problems and how to build a connected supply chain. According to Jos, the disconnected supply chain is a big problem and companies have very inefficient ways to exchange data in the supply chain. From emails, Excel, and File sharing to developing a single standard to exchange data, supply chain management remains a big problem. Here is an interesting passage. A traditional approach is to have suppliers work in so-called “bespoke portals” which causes the supplier to have a separate environment for each OEM.
Of course, the traditional industries that invented PLM have invested in a kind of connected supply chain. However, is it really a connected supply chain? Aerospace and Defense companies had their supplier portals. A supplier had to download their information or upload their designs combined with additional metadata.
These portals were completely bespoke and required on both sides “backbreaking” manual work to create, deliver, and validate the required exchange packages. The OEMs were driving the exchange process. More or less, by this custom approach, they made it difficult for suppliers to have their own PLM environment. The downside of this approach was that the supplier had separate environments for each OEM.
A more connected PLM approach is to bring a supplier to work directly into OEM’s PLM environment.
The ultimate goal in the long term will be the connected supply chain. Information shared between an OEM, and a supplier does not require human-based interfaces to ensure everyone works with the correct data. The easiest way and this is what some of the larger OEMs have done, is to consider suppliers as part of your PLM infrastructure and give them access to all relevant data in the context of the system, the product, or the part they are responsible for. For the OEM, the challenge will be to connect suppliers – to motivate and train them to work in this environment. For the supplier, the challenge is their IP management. If they work 100 percent in the OEM environment, everything is exposed. If they want to work in their own environment, there is probably double work and a disconnect.
Security plays an important role in the organization of supply chain management and supply chain models and business processes. Supply chain managers are very sensitive to who and how will get access to the data in supply chain processes. Therefore product lifecycle management system is key to having this data organized well and having a continuous flow model of data exchange.
The most promising approach is to have a cloud environment with shared space that allows to both OEM and suppliers to work on the same data. This brings me to the need of having multi-tenant PLM architecture, which is capable to organize such a network layer to keep data shareable and at the same time, allows to every company to manage the IP in their own tenant, to have full administration and capabilities to manage and share data.
3 PLM System Architectures For Supply Chain
So, what are available PLM architectures for supply chain management and how modern PLM architecture can improve supply chains, and what supply chain model is the best for modern digital product lifecycle management? Let’s speak about three possible PLM Supply Chain Architectures.
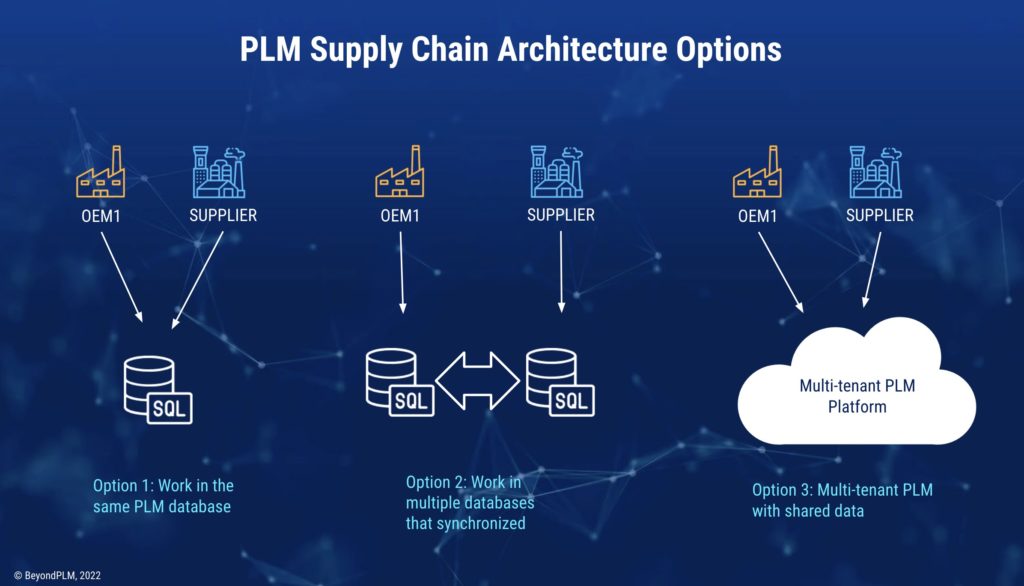
Option 1: Work in the same PLM database
This option is a popular solution and is used a lot in production these days. Usually popular for industries with tightly coupled OEM and supplier coordination. Basically, it means each supplier works in the same PLM database. OEM IT defines access control for each supplier (based on roles or projects). The disadvantage for OEM is to provide a PLM system to all suppliers. The disadvantage for the Supplier is to have such a PLM system for all OEMs. Might be not a very scalable option in both cases.
Option 2: Work in two PLM systems that are synchronized
Such an option is used very often when OEM doesn’t work to give suppliers access to their centralized PLM and put another system (eg. in DMZ) which is sync data from the central database to the outside one. The disadvantage for OEM is maintenance. The disadvantage for suppliers is the same as before – separate environments.
Option 3: Multi-tenant PLM system
This is the most promising option because multi-tenant PLM has its own network layer that allows it to share data in a granular way and share exactly the data that is needed. The advantage of the system is to simplify data sharing while providing to each company its own admin and tenant to manage data.
What is my conclusion?
The manufacturing industry is on the path of digital transformation and looking for efficient solutions to connected systems capable to share data instantly in real-time and provide a modern environment to manage and administer multiple companies – manufacturers and multiple supplier levels. While a single PLM system is a reliable old architecture, it brings a lot of issues with robustness, management and security. The modern multi-tenant system approach brings new technologies to solve PLM and supply chain management problems. Just my thoughts…
Best, Oleg
Disclaimer: I’m co-founder and CEO of OpenBOM developing a digital cloud-native PDM and PLM platform that manages product data and connects manufacturers, construction companies, and their supply chain networks. My opinion can be unintentionally biased.
The post PLM System Architecture For Digital Supply Chain appeared first on Beyond PLM (Product Lifecycle Management) Blog.
Be the first to post a comment.