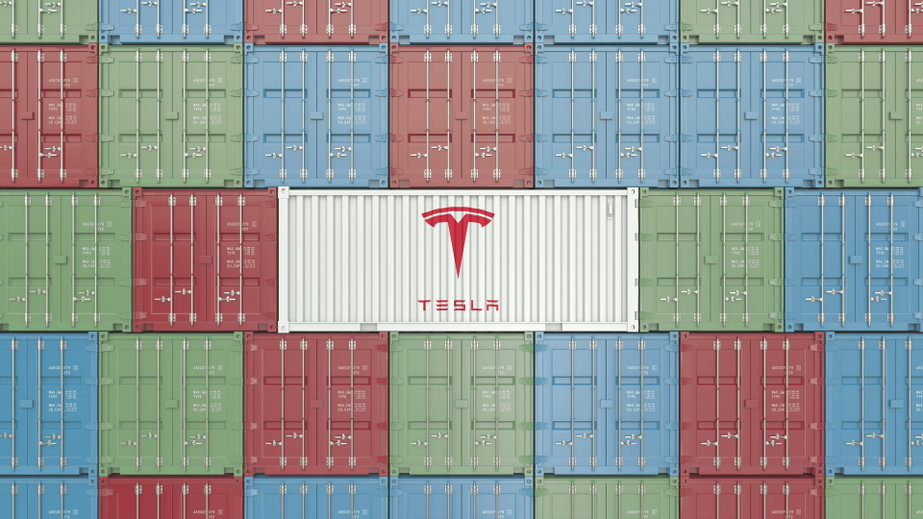
It’s no secret that the manufacturing industry is in a state of flux. Manufacturers are under pressure to keep up with changing technology and consumer demands, all while contending with a shortage of skilled workers and continuously growing challenges with their supply chains. Learning from innovative companies and outliers is one of the things that help to predict future trends. Almost a decade ago, I wrote the article – Will Tesla Develop Their Own PLM System? Already 10 years ago, Tesla made a conclusion that the speed and agility of Tesla make traditional business systems (eg. SAP and similar) not applicable. Tesla was developing their own IT systems.
How Tesla Soared Despite Supply Chain Crisis
Getting back to the supply chain, my attention was caught by the NYT article – Why Tesla Soared as Other Automakers Struggle To Make Cars. Here are a few interesting passages from the article.
G.M. and Ford closed one factory after another — sometimes for months on end — because of a shortage of computer chips, leaving dealer lots bare and sending car prices zooming. Yet Tesla racked up record sales quarter after quarter and ended the year having sold nearly twice as many vehicles as it did in 2020 unhindered by an industrywide crisis.
Tesla, which rarely answers questions from reporters, did not respond to a request for comment for this article. It has said little publicly about how it managed to soar in a down market.
We have used alternative parts and programmed software to mitigate the challenges caused by these shortages,” the company said in its third-quarter earnings report. The performance is a stark turnaround from 2018 when Tesla’s production and supply problems made it an industry laughingstock. Many of the manufacturing snafus stemmed from Mr. Musk’s insistence that the company make many parts itself.
Other car companies have realized that they need to do some of what Mr. Musk and Tesla have been doing all along and are in the process of taking control of their onboard computer systems. Mercedes, for example, plans to use fewer specialized chips in coming models and more standardized semiconductors, and to write its own software, said Markus Schäfer, a member of the German carmaker’s management board who oversees procurement.
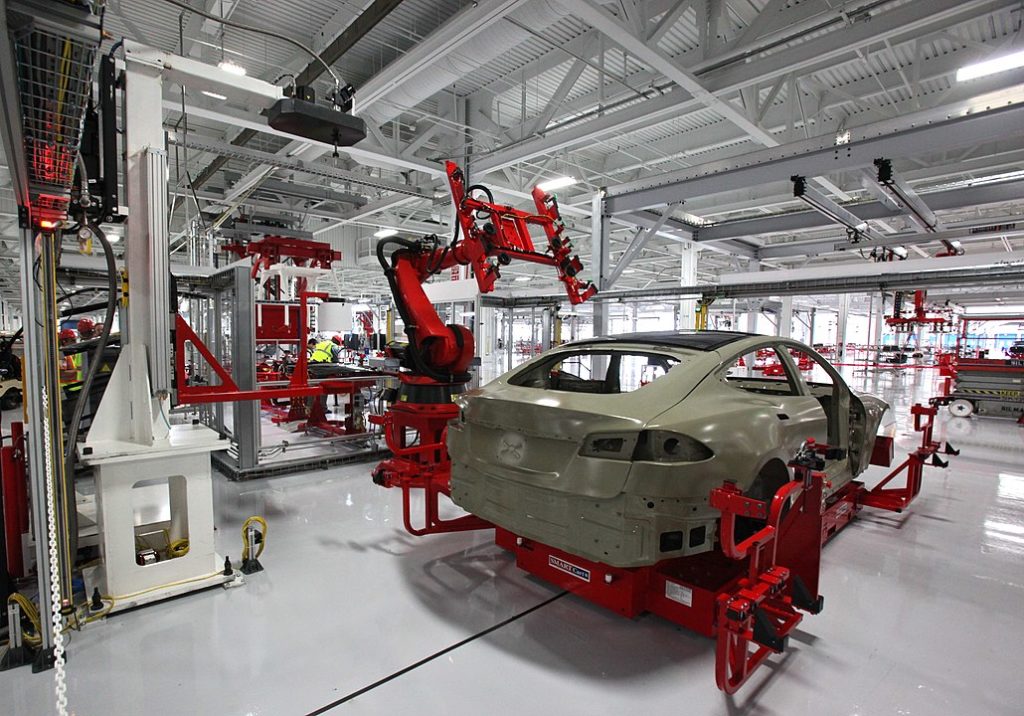
Unique Inventory Management Solution
Intuit Quickbooks blog article from 2014 speaks about Tesla’s business and data management solutions that helped them to develop a unique supply chain management system. Check this article – Tesla Supply Chain – Custom-build World Class Supply Chain. The article is worth reading. It speaks about Tesla’s decision to take ownership of its supply chain management. Tesla’s challenges are very similar to many small businesses. While Tesla is not a small company, it cannot use the same economy of scale that is available to large car automakers. While so, the innovation comes in place. Here is another passage:
To try and minimise risk, they keep very little inventory, choosing instead to place most of their customers on a several month long waiting list. Tesla admits that there is little research on the impact of this sales model on consumer demand. So far, there’s been inadequate data to support any conclusion regarding the loss of business due to the wait time.
However, there are also significant upsides to this practice. By keeping little inventory and essentially producing on demand, Tesla can minimise the amount of capital and risk tied up with storing excess inventory. In addition, the wait encourages additional customisation, a premium that many of their paid customers might not have chosen to pay for if they could immediately drive a stock car off the lot.
Tesla built a unique inventory management system, which corresponds to the same article I mentioned at the beginning – Tesla built their own IT.
What Other Manufacturers and PLM Vendors Can Learn From Tesla?
It is very interesting to learn from Tesla and, especially, how to apply Tesla’s strategies to other places in the manufacturing world. The unique supply chain and inventory management solution allowed Tesla to leverage the economy of scale that only was available to very large players in the automotive industry. I speak mostly for SME manufacturing companies and the opportunity to introduce unique integrated PLM and ERP solutions capable to undermine big businesses. These solutions can help manufacturing companies navigate an increasingly complicated business world with huge challenges in supply chain management.
Online integrated data management systems capable to manage an entire supply chain system with the engineering and product life cycle management components integrated with supplies data and flexibility to control and share the data between multiple companies in the supply chain in real-time. PLM vendors own one of the most interesting parts of the information – product and engineering data. This is the foundation of every manufacturing business. The data help to decide what alternative components can be used in the supply chain or what changes are needed to be done in design and engineering to fit the alternative supply components. This combination of engineering, inventory, and supply chain data can bring the intelligence that no one in the manufacturing world has today. Similar to how the internet and online applications empowered individual consumers, a new generation of engineering and manufacturing software will empower OEMs of different sizes and help them to scale their supply chains at the time of crisis.
What is my conclusion?
Practically a century ago, Ford Motors demonstrated the innovation of vertically integrated manufacturing plants and how it can be more efficient to produce vehicles from rubber, steel, and glass in a single factory. Interestingly enough, Tesla’s supply chain management innovation can be considered as a way back to Ford’s approach of taking responsibility for all components of supply chain management. Here is the thing – the internet and modern engineering and manufacturing software can turn Ford’s and Tesla’s innovation into a virtual space. By using integrated product data management services combined with inventory and supply chain control, OEMs can build resident supply chain solutions. The foundation of these solutions is a data integration of all processes together. The core element of this solution is modern data management with integrated items, BOM, and inventory management as a service. In the next few articles, I will talk more about the elements of these solutions. Tesla’s innovations show the way to many other manufacturing companies of different sizes. Just my thoughts…
Best, Oleg
Disclaimer: I’m co-founder and CEO of OpenBOM developing a digital network-based platform that manages product data and connects manufacturers, construction companies, and their supply chain networks. My opinion can be unintentionally biased.
The post Will Tesla Lead The Way To Future Supply Chain And Engineering Intelligence in Manufacturing? appeared first on Beyond PLM (Product Lifecycle Management) Blog.
Be the first to post a comment.